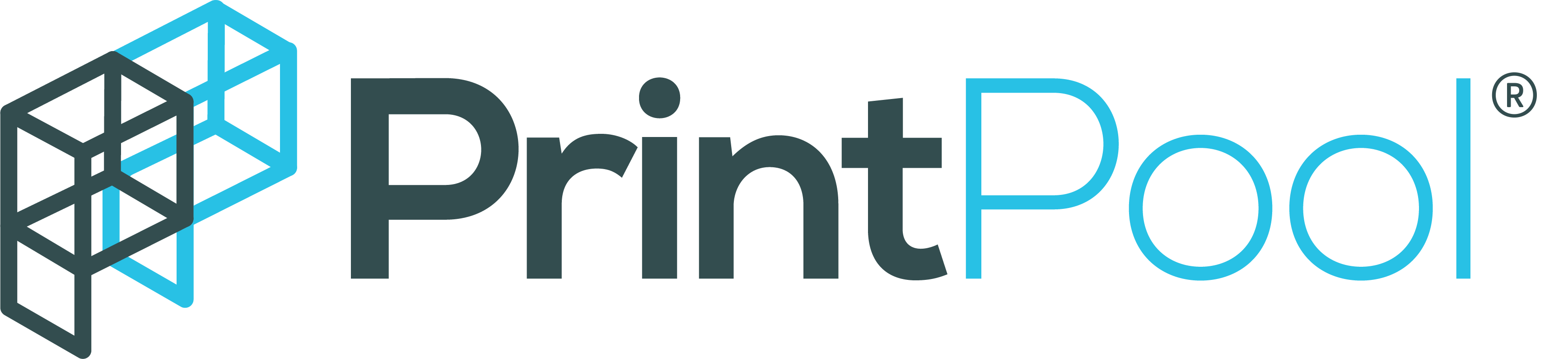
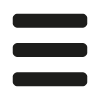
We have a range of large-format and smaller resin 3D printers, which can be used to manufacture your designs with exceptional surface finish and materials properties. The largest possible part size is 335 × 200 × 300 mm.
Hole Size
> 0.8mm
Overhangs
> 60 degrees
Wall Thickness
> 1.2mm
Emboss/Engrave
0.6mm width
0.4mm depth
Bridging
<6mm
Clearance
0.1mm Tight
0.2mm Loose
We offer both regular resin 3D printing and large-format resin 3D printing, so no matter the size of your design you can get an accurate prototype on your desk in just a few days.
Our SLA resins offer excellent mechanical properties for complex parts, and have a wonderfully smooth and consistent surface finish. Use SLA materials for visual models, that mimic the appearance of injection moulded parts, as well as functional prototyping.
A smooth and hard material, with a satin, matte surface. Perfect for 'looks like' prototypes that need a near injection moulding finish.
Standard ResinA nearly completely transparent material, for prototyping optics, and for parts where fluid flow needs to be observed within a component.
Clear ResinA certified skin-safe material, with a balanced combination of stiffness and durability. For general engineering prototypes, with a bit of flex.
Tough 1500 ResinAn extremely tough material, that can be used to mimic polypropylene. Has the lowest coefficient of friction of any of our materials, and is slightly flexible.
Durable ResinFlame retardant resin has UL 94 V-0 blue card certification and can be successfully used for a wide variety of different engineering applications.
Flame Retardant ResinPrintpool offers a range of professional 3D printing services to engineers and product designers across the UK. We provide a world-class additive manufacturing service, and unlike many competitors, are happy to discuss your application in detail and answer any questions you might have. We will sometimes recommend small design changes if we think that it will improve the end result!
Stereolithography (SLA) 3D printing is a process involving VAT photopolymerisation - which is where a liquid resin (photopolymer) turns solid when hit with UV light from a laser. It is the second most common type of additive manufacturing after FDM 3D printing, and is sometimes known more generally as 'resin printing'.
To create parts, a metal build platform (build plate) is lowered into a resin tank with a transparent bottom, and covered with any one of a number of SLA resins. A low powered laser is then shone onto the material, in a precisely controlled pattern that matches the cross-section of the part being printed. The build platform then moves up a little, allowing more liquid to flow onto the (now solid) layer above, and the process repeats, so that a fully solid part builds up in layers. SLA 3D printing is known for its exceptional quality prints, high resolution, smooth surfaces, and ability to capture very fine details.
Although similar, SLA should be not confused with Digital Light Processing (DLP). DLP printing uses an LCD screen as its light source, and sometimes even hardens parts using light in the visible part of the electromagnetic spectrum. Digital Light Processing has its advantages, but parts often have lower detail, due to the fixed pixels on the screen translating to fixed voxel sizes in 3D. Both types of 3D printing excel at producing complex geometries and high resolution functional parts, however.
As SLA machines are able to produce printed parts with a smooth surface finish and complex features, resin 3D printing is one of the few additive manufacturing techniques with print quality that can match traditional manufacturing processes such as injection moulding. This makes it perfect for when high quality parts and prototypes are needed for client presentations, and to demonstrate how a product will look when ready for mass production.
Complex geometries are also achievable, including custom parts with small or intricate features that would be impossible to manufacture using any other methods. In particular, resin 3D printing excels at producing complex internal channels for fluid flow, which can be very difficult to make using traditional tools.
SLA printing works with a wide variety of different materials - each with different mechanical properties. Using durable and tough photopolymers, we can produce functional parts with better accuracy and detail than on a selective laser sintering (SLS) or Fused Deposition Modelling (FDM) 3D printer. It is also the only technology that can produce high transparency clear parts.
SLA material properties vary more widely than any other process we offer. If you're unsure exactly what material would be best, get in touch and we can help.
In general, the more brittle the SLA material used, the higher the accuracy. Our more tough and durable resins compromise slightly on precision, but are still able to capture fine details.
Generally with SLA parts, one side is supported and the other isn't. We will orient the part so that the more aesthetically important side has no support marks.
The SLA printing process is inherently more complex than some other additive manufacturing techniques. Once the SLA printer has finished, each printed part must be washed thoroughly in Isopropyl Alcohol by a Printpool engineer, and then 'post-cured' using a UV oven, to fully solidify the material ready for use. In addition, the materials used by a resin 3D printer are irritants before they have been cured by the laser beam during the additive process. This can increase the lead time, and makes SLA parts more expensive than they otherwise would be, due to the extra steps and precautions we must take to stay safe.
Parts printed from SLA materials generally have lower temperature resistance, and poorer thermal properties than other 3D printer materials. The print speed is also slower in some case, meaning they can be less useful for rapid prototyping than other options. This does depend on the layer height chosen, and how full the build volume is however.
Designing for the stereolithography process is complicated. Unlike with some other types of 3D printing, the support structures underneath an SLA printed part are not just designed to resist gravity, but also other forces generated during the print process. At Printpool we use low-force stereolithography, which reduces the effect, but without some expert knowledge its hard to know exactly which parts of your design will need a support structure underneath, making designing for SLA difficult.
We advise trying to remove sharp edges from your parts, as these can encourage stress concentrations to form, which will weaker your final 3D print. Also, no area of the design should be thinner than 0.5mm, as this may not build properly. We have further, more detailed advice in our resources pages.
Many people don't realise that SLA 3D printing was actually the first type of additive manufacturing technology to be developed. On March 11, 1986, Chuck Hull first patented the 3D printing technology, with his “Apparatus for Production of Three-Dimensional Objects by Stereolithography”. He had the idea after using UV light to harden tabletop coatings three years earlier. 3D systems, a very well known 3D printing company, developed SLA 3D printing for many years under Hull's leadership, before a number of other players entered the market. Most notably, Formlabs launched a series of excellent high resolution desktop SLA printers, that offered huge cost savings over the more expensive industrial SLA offerings from 3D systems. This led to a surge in new resin desktop printers from other manufacturers.
The rise of good quality cad software has also made SLA 3D printing more useful, as before this point the 3D printing wasn't used in rapid prototyping workflows, as there was no data available from which to print! Advances in chemical engineering have increased the number of materials available, and now there are flexible, durable, stiff, glass-filled and castable resins on the market, that can be used for high resolution 3D printing of just about anything.
Other types of VAT photopolymerisation 3D printers have appeared over the years, mostly differentiated from SLA by a different resin vat, light source, printing volume, and/or chemistry. All offer high resolution, require support structures, and require significant post-processing, contrasting against other technologies like selective laser sintering.
At Printpool we exclusively use the Formlabs Form 3 printers, for all our SLA printing. They offer outstanding finish and high resolution in a wide range of materials, and are more highly tested and optimised than many types of much more expensive industrial SLA printers.
Unlike some other technologies, SLA 3D printers produce parts that are entirely solid. Parts are also more isotropic (the same mechanical properties in all directions). Parts with large solid areas should usually be hollowed in CAD software to save money and reduce peeling forces however.
We will always wash, post-cure, remove support structures, and gently sand every print, to improve the surface where the supports were. When you receive your print, no further finishing should be needed for the vast majority of applications.
Choosing what process to use for each print is critical. Generally, larger and less complex shapes are better suited to FDM 3D printers, whereas smaller, more complex designs are better suited to resin 3D printers. Deciding on the best option is complex, however, so feel free to reach out to us for help with this.
If you wish to send multiple design files, please put them in a zip folder first! Our website will only accept a single file.
If you require 3D scanning services, please include a picture of the object you need to be scanned.