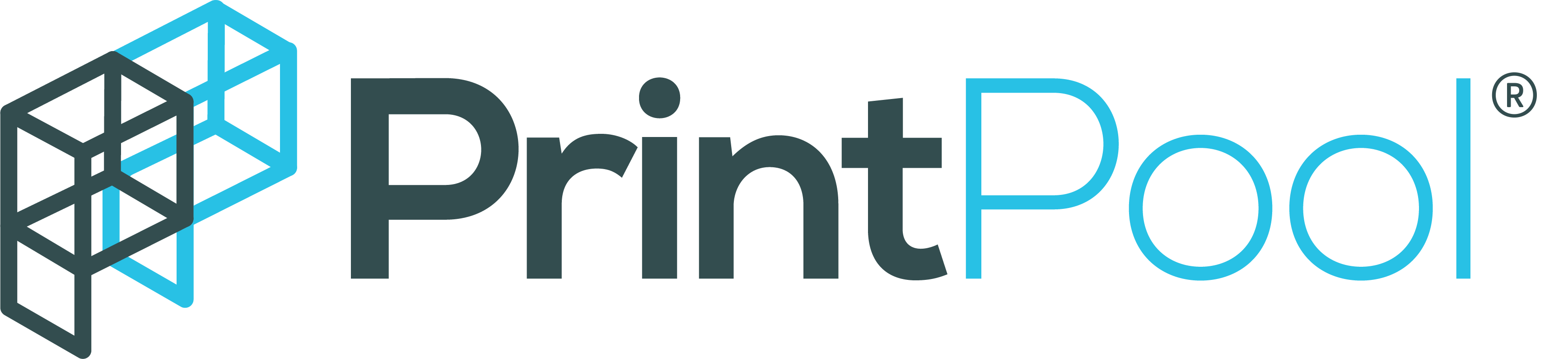
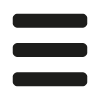
We have a range of large professional FDM 3D printers, which can be used to manufacture prototype and production components. The largest possible part size is 330 x 240 x 300 mm.
Hole Size
> 1.5mm
Overhangs
> 45 degrees
Wall Thickness
> 1.5mm
Emboss/Engrave
1.5mm width
0.8mm depth
Bridging
<10mm
Clearance
0.15mm Tight
0.25mm Loose
We offer both large format and smaller FDM 3D printing, so no matter the size of your design you can get an accurate prototype on your desk in just a few days.
Our FDM materials make an excellent starting point when first testing out 3D printing, and how it fits within your design process. These materials are cost-effective and have a good balance of toughness, stiffness, and surface quality. For general prototyping and proof-of-concept prints, we recommend either Tough PLA or Recycled PLA. Consider PET-G if these aren't suitable for your project, perhaps due to their low heat resistance.
A tougher version of PLA with properties closer to those of ABS. An excellent prototyping material, with slightly better quality than Recycled PLA.
Tough PLAA recycled bioplastic material made from factory waste streams. Perfect for large models, first prototypes, and available in a range of colours.
Recycled PLAPET-G is a strong and hard general prototyping material that has a little bit of flex. It is UV resistant and withstands higher temperatures than PLA.
PET-GPrintpool offers a range of professional 3D printing services to engineers and product designers across the UK. We provide a world-class additive manufacturing service, and unlike many competitors, are happy to discuss your application in detail and answer any questions you might have. We will sometimes recommend small design changes if we think that it will improve the end result!
FDM stands for Fused Deposition Modelling (sometimes called Fused Filament Fabrication or extruder printing). In this process, molten material is extruded from a heated nozzle in a precise pattern on top of the previous layer, leaving a layer of solidified material, that is then in turn built on by the next layer. By repeating this process, a part is slowly built up, from bottom to top, in thin slices. Thermoplastic materials of all kinds are available in filament form (to feed into the nozzle) for this process. FDM printing is one of the most low-cost and versatile additive manufacturing processes, capable of producing functional parts, as well as general rapid prototyping.
Cheap FDM 3D printers are quite widely used by consumers and hobbyists, and so this process is most likely the one you first picture when someone says the word '3D printer'. Professional FDM printers are very different from a consumer FDM 3D printer, however, primarily in terms of print quality, but also dimensional accuracy, and compatibility with advanced materials. We can print in a number of high-temperature and custom materials that would be impossible using most cheaper machines. Our FDM machines also have a second printhead that can use soluble and breakaway supports, which are required on certain designs that have overhangs and complex geometry.
Interestingly, the majority of our customers already own their own 3D printer. Although many 3D printing sales teams may disagree, it is almost impossible to get one machine that can do everything you might need it to, unless you work in a very narrow design niche. The majority of engineering workshops and product design studios will produce a wide variety of different types of parts, depending on what work is happening at the time. Most studios simply don't have the budget, physical space, trained staff or software to run the right range of different FDM 3D printers in-house.
The FDM 3D printing process starts by setting up the build in a software program, sometimes called a 'slicer'. A 3D model of each part to be printed is loaded into a virtual representation of the build volume of the 3D printer, and each part is orientated in the optimum position. Many parts can be made on a single FDM 3D printer at once. The final result can be previewed in a virtual environment before starting the 3D printing process, allowing the operator a chance to spot any potential errors or issues.
FDM technology is a very widely used rapid manufacturing process, and so a broad range of different thermoplastic polymers are available and have been optimised as a feedstock material. This has driven down material prices, and so plastic filaments are now very cost-efficient.
Using the second extrusion head on our desktop machines, we can even FDM 3D print using two different polymers, or two different colours of the same polymer, at the same time. This opens up many exciting possibilities for complex multi-material parts and multi-coloured prototyping. The material extrusion process itself is low mess and low hassle, especially when using industrial FDM printers that typically have automatic bed levelling and an easily swappable build platform. Our machines produce high-quality parts every day with very little maintenance, and are very fast, perfect for rapid prototyping.
Due to the simple nature of the process, large models and functional prototypes are easy to produce on an FDM 3D printer, when compared to other technologies. The build volume, or print volume, of our largest FDM printers, is far greater than either our SLA (Stereolithography) or SLS (Selective Laser Sintering) machines. This is mainly because the printing process doesn't feature lasers, and is based on a simple cartesian coordinate system, making it more scalable.
FDM 3D printing has the most visible layer lines of any process that we offer. For fine details and smooth curved surfaces, consider SLA 3D printing as an alternative.
Any section of your design which overhangs the build plate will need support, which may affect the surface finish.
For general prototyping, Tough or Recycled PLA is usually the best material for the job. If chemical, heat, UV or wear resistance is important, consider PET-G.
Due to the way the melted material is deposited, FDM parts have a distinctive layered appearance when viewed from the side. How visible this mainly depends on the layer thickness, or layer height, that was chosen in the slicing software during the setup process. All else being equal, a larger layer height results in a less smooth finish, but this can sometimes be improved by sanding 3D prints as a post-processing step. The minimum layer height we can use at Printpool for FDM printing is 0.1mm.
Large, flat 3D prints can sometimes warp, due to the way that a thermoplastic material cools more rapidly in some areas than others. This is the primary reason we don't use ABS (Acrylonitrile butadiene styrene) which is a very common material for injection moulding and instead rely on different high-performance materials such as PET-G, that have many of the same properties, but with less tendency to warp. One reason that PLA filament is so excellent for 3D printing is that the low melting point of the bio-plastic material results in far less warpage than other materials.
Parts made on an FDM machine may require support structures. Although we use both breakaway and dissolvable supports to minimise the effects, this generally worsens the surface finish on the areas of the part that contact the support.
FDM prints are always anisotropic, meaning that the properties of the engineering materials we use are slightly different in each direction. In particular, components that are placed in tension along the z-axis, perpendicular to the build platform, are more likely to fail as the object delaminates. This effect can be more or less pronounced with different materials, depending on their properties.
Design for manufacture is always important when approaching a project, and this is no different in the world of digital manufacturing. Design for Additive Manufacturing (DfAM) is covered more broadly elsewhere, but in the context of FDM 3D printing, there are a few key ideas to bear in mind.
An overhang is a surface that is at an angle of less than 45° from the build plate. Material extrusion into empty space, without a surface on which the plastic can adhere, results in either a failed part or a very rough surface finish. Support materials are used to provide something to print onto, but these add unnecessary cost and complexity, as well as additional post-processing steps.
It is best practice to design parts whilst visualising where they will sit within the build volume of the 3D printer. With this in mind, areas at a shallow angle to the build platform can be altered or removed. Unlike most other 3D printing processes, FDM parts build best when they have a large flat surface in contact with the build plate. Machine operators will often orientate the largest flat surface this way during the setup process, so bear this in mind when designing your part.
FDM 3D printing has come a long way since the original patent, owned by Stratasys, expired in 2009. Soon after, there was a big surge of new FDM 3D printing machines released onto the market, as companies began taking advantage of their newfound freedom to design machines that deposited molten plastic layer by layer. This was a good thing for the field of additive manufacturing, as it encouraged a huge amount of new innovation that wasn't possible before.
There was a big culture of open-source designs, including the widely-known RepRap movement, which grew out of the desire to 3D print parts for new 3D printers. By the early 2010s, 3D printing became widely known about by the general public, and was at the peak of the Gartner hype cycle. This was around the time that 3D-printed 'guns' appeared in the news, causing a lot of controversy.
The downside of this period of rapid growth was that the early attempts at the FDM printing process were mixed, and a lot of the parts and objects produced by those machines were of quite poor quality. This should be expected from an early-stage technology, but many engineers and product designers were disappointed by the surface finish and material properties on offer and turned their backs on additive manufacturing. Stratasys, who has 20 years to perfect the technology, still offered by far the best FDM printers at this time, and rapid prototyping was the only serious use-case for FDM 3D printing.
Ten years later, a lot has changed. The FDM 3D printer has evolved from a desktop toy into a serious manufacturing technology, compatible with serious engineering-grade polymers. Stratasys no longer has such a stranglehold on the FDM 3D printing market, and there are now a bewildering array of different types of extruder printers, including belt 3D printers, large format options, and the bizarre-looking delta printer.
New players in the 3D printing market have appeared, such as Ultimaker and Markforged, and their phenomenal growth is a testament to the quality of the machines that they produce. That being said, the quality improvement of 3D printed parts from even the cheapest FDM printer has been phenomenal, and the wider engineering and design world is all the better.
Components that come off the FDM printer are almost never solid, no. There are a few layers of solid material on the top and bottom of the part, called roof and floor layers. There are also a few solid layers on the sides of the part, called walls. Inside this is a lattice structure, which is called the infill. We make this 40% solid on most engineering components, and 20% solid on cosmetic or aesthetic models.
Sometimes. Any FDM filaments supplied by you would need to be compatible with our printers (2.85mm diameter), and of high enough quality that we can be confident of a good result. We refuse to print objects using poor-quality materials.
We will always remove supports and unsightly blemishes from each part before the order is completed. Where parts have been heavily supported, there may be some 'scarring' visible on the surface, however.
Choosing what process to use when printing your design is critical. Generally, larger and less complex shapes are better suited to FDM 3D printing, whereas smaller, more complex designs belong to SLA or resin 3D printers. Deciding on the best option is complex, however, so feel free to reach out to us for help with this.
If you wish to send multiple design files, please put them in a zip folder first! Our website will only accept a single file.
If you require 3D scanning services, please include a picture of the object you need to be scanned.