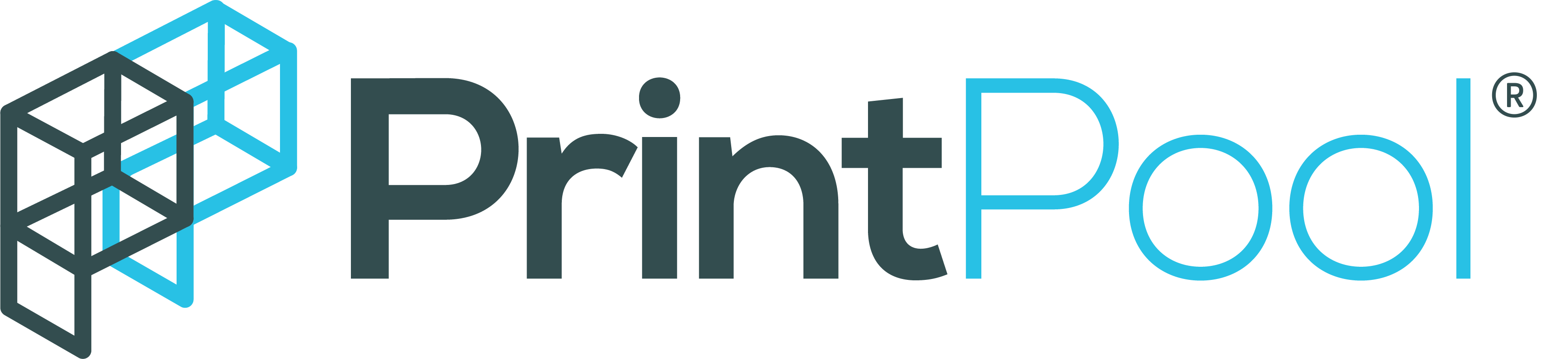
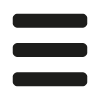
We run specialty 3D printers by Markforged, which use a special blend of nylon and carbon fibre. This material can also be reinforced with additional continuous fibreglass. The largest possible part size is 320 x 132 x 154 mm.
Hole Size
> 1.5mm
Overhangs
> 45 degrees
Wall Thickness
> 1.5mm
Emboss/Engrave
1.5mm width
0.8mm depth
Bridging
<10mm
Clearance
0.15mm Tight
0.25mm Loose
Parts made with CFR 3D printing can be reinforced with continous fibreglass. Reach out to us to discuss whether this would be suitable for your design.
Our CFR 3D printing materials offer outstanding strength, stiffness and durability, while retaining high dimensional accuracy. CFR parts build using a blend of carbon fibre and nylon, which can then be further reinforced using continuous fibres such as fibreglass. Use these materials for serious engineering applications, jigs, fixtures, and end-use parts.
A blend of nylon and carbon fibre, for demanding applications. Excellent dimensional stability, surface finish and heat resistance.
OnyxOnyx on steroids. Continuous glass fibre is added in select locations to maximise the strength, stiffness and durability of this already outstanding material.
FBGR OnyxPrintpool offers a range of professional 3D printing services to engineers and product designers across the UK. We provide a world-class additive manufacturing service, and unlike many competitors, are happy to discuss your application in detail and answer any questions you might have. We will sometimes recommend small design changes if we think that it will improve the end result!
Continuous Fibre Reinforcement (CFR) is an advanced type of 3D printing that can produce composite 3D printed parts, by selectively depositing continuous fibres in areas of a component that experience high stress. CFR 3D Printed parts can rival the strength of aluminium at a fraction of the cost and weight.
The plastic material that is used as a matrix, is based on Nylon, with short-chopped carbon fibres added to give better stiffness and strength. This material is Onyx, and has outstanding wear, heat and chemical resistance. Onyx parts also resist degradation in UV light.
The placement of the continuous fibres in a CFR 3D printed part is critical. Only areas of high stress, or that need to be particularly stiff, should be reinforced. This is not just to save cost, but also reduce manufacturing time, and take full advantage of the properties of the base material, Onyx.
The main advantage of CFR components is the exceptional strength, durability and general material properties that the material offers. Producing strong parts at a low weight is just one benefit though.
Due to the highly refined printhead, which uses a hardened steel nozzle, the surface finish found on Onyx parts is outstanding. The layer lines are virtually invisible, when compared to FDM printing, and have a consistent, matte black finish that looks professional and refined.
As with other additive manufacturing, complex geometries are easy to 3D print, and the dimensional accuracy that this process can achieve is superior to both FDM printing and SLA printing in our experience.
CFR 3D printing works by selectively reinforcing key areas of a component. Knowing which areas require strengthening is crucial.
When considering a part for CFR printing, it is important to know in which orientation in will be printed. CFR parts are anisotropic, and will require supports on overhangs.
If you are after a prototype part, that doesn't require high strength, it would usually be better to go for a cheaper FDM print instead, to save money.
The CFR process is complex, and the materials used are more expensive than FDM materials or SLS materials. SLA materials are approximately the same price, but as CFR parts tend to be larger, they are often more pricy than some users expect.
As with FDM 3D printing, overhangs need to be supported in order in print successfully. No dissolvable supports are available when printing using CFR, and so supports made from Onyx are used. These are easily removed from the part by Printpool prior to dispatch however.
Parts printed from CFR materials generally perform very well. Bear in mind that the inside volume of an given part will not be solid however, and will consist of a lattice structure infill. Customers can request specific infills, and how solid the inside should be. By default, we use a 34% solid infill.
Designing for the CFR process is very similar to designing for the FDM Printing process. The key ideas revolve around reducing the number of overhangs, and including a flat surface somewhere in the design that can be used as a stable base.
We advise trying to remove sharp edges from your parts, as these can encourage stress concentrations to form, which will weaker your final 3D print. We have further, more detailed advice on our resources pages.
CFR 3D printing is a relatively new innovation, developed by Markforged, a US based company founded in 2013. A couple of years later, in 2015, a few leading engineers and leaders from Markforged left the company, and formed a rival firm - Desktop Metal. Desktop Metal offers a 3D printing ecosystem that is similar in many ways to the technology offered by Markforged, and indeed the two companies have had a lot of bad blood, including a number of lengthy legal battles.
Each claims that the other has stolen proprietary information, and disparaged the technology of the other, during this process, despite repeated settlements.
Luckily, despite the leaders of each company behaving like small children, the engineers and designers at both companies continue to produce outstanding 3D printers. We use Markforged products as we believe they have a slight edge in terms of capabilities and quality.
At Printpool we think that fibreglass offers a better cost/benefit ratio than carbon fibre. Reinforced carbon fibre parts are even stronger and stiffer than fibreglass ones, but almost prohibitively expensive.
Although less scalable than SLS 3D Printing, CFR production runs are possible, and we have done this for customers in the past. It really depends on the size and shape of the component.
CFR printing should be considered any time you need a component to have strength and durability that can't be gained any other way. Some customers also choose CFR printing for its exceptional surface finish.
If you wish to send multiple design files, please put them in a zip folder first! Our website will only accept a single file.
If you require 3D scanning services, please include a picture of the object you need to be scanned.