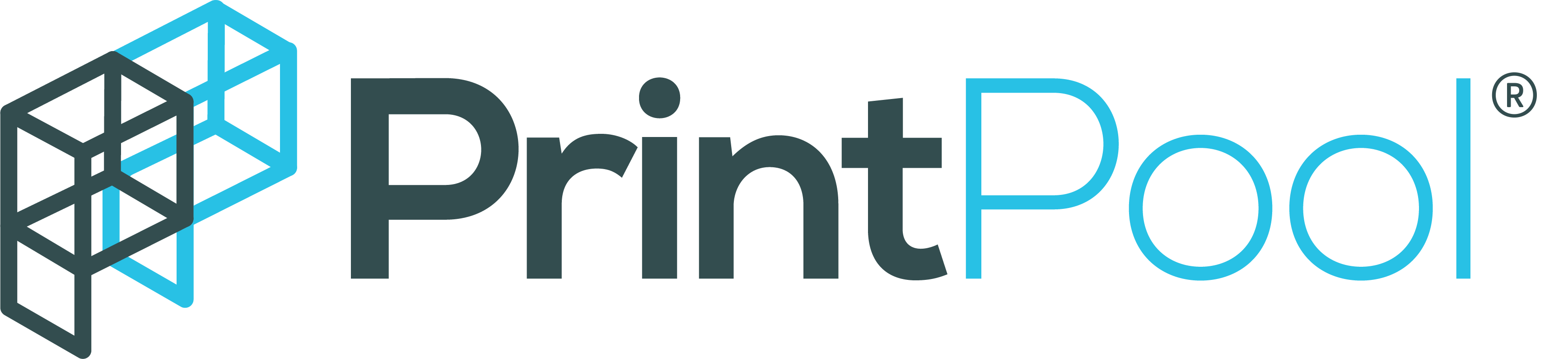
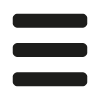
The largest we can print in one piece is approximately 330 x 240 x 300 mm. This is using our FDM process, in Tough PLA, Recycled PLA, or PET-G. It is sometimes possible to print larger items, by printing the part in multiple pieces and joining them together afterwards. This is usually best suited to aesthetic pieces rather than structural ones though.
ABS is a hateful material to 3D print. It gives of unpleasant fumes when printing and everyone gets a headache. Even if it prints well, the material properties of 3D printed ABS aren't the same as injection moulded ABS anyway, which defeats the point for most of our customers. As an alternative, we recommend Tough PLA, Tough 1500 Resin, or Onyx usually -depending on the application.
It depends! Our pricing is primarily based upon the volume of material used, so larger items cost more than smaller ones. Our most premium material, FBGR Onyx costs about 5x as much as our cheapest, Recycled PLA. Try our pricing calculators on our Get A Quote page to get a better idea, or just reach out to us for a personalised quote. Our minimum order charge is £45.00 + VAT.
Right now we don't offer any metal options, but we're looking into it, and trialling some possibilities. We won't offer anything until we're happy the metal materials meet our high standards of quality and service. Watch this space.
We use the two terms interchangeably, as does the vast majority of the wider industry. Strictly speaking though, there is a difference. '3D printer' is a trademarked phrase, owned by Stratasys, so the wider industry had to come up with an alternative. Additive manufacturing is a broader term encompassing all manufacturing technologies that 'add' material, usually in layers, to make a 3D shape.
Sometimes we can, yes. If you provide your own materials then we can often use them, so long as they are compatible with our machines, and are of high enough quality. Alternatively, for a small surcharge we can often buy in custom materials specially for your order.
Choosing the right 3D printing material is critical to achieving the best result, but is very tricky to get right without lots of experience. Luckily, we have that. Reach out to us and we will discuss your exact requirements and recommend the bets options.
Every order comes with next day delivery as standard, and at no extra cost. We use Royal Mail for all deliveries unless you specifically request an alternative courier. If you would prefer to pick up your order in person however, this can be arranged - just let us know before we post it! You must arrange all visits with us though, so please don't stop by unannounced.
Components that come off the FDM printer are almost never solid, no. There are a few layers of solid material on the top and bottom of the part, called roof and floor layers. There are also a few solid layers on the sides of the part, called walls. Inside this is a lattice structure, which is called the infill. We make this 40% solid on most engineering components, and 20% solid on cosmetic or aesthetic models.
Sometimes. Any FDM filaments supplied by you would need to be compatible with our printers (2.85mm diameter), and of high enough quality that we can be confident of a good result. We refuse to print objects using poor-quality materials.
We will always remove supports and unsightly blemishes from each part before the order is completed. Where parts have been heavily supported, there may be some 'scarring' visible on the surface, however.
Choosing what process to use when printing your design is critical. Generally, larger and less complex shapes are better suited to FDM 3D printing, whereas smaller, more complex designs belong to SLA or resin 3D printers. Deciding on the best option is complex, however, so feel free to reach out to us for help with this.
At Printpool we exclusively use the Formlabs Form 3 printers, for all our SLA printing. They offer outstanding finish and high resolution in a wide range of materials, and are more highly tested and optimised than many types of much more expensive industrial SLA printers.
Unlike some other technologies, SLA 3D printers produce parts that are entirely solid. Parts are also more isotropic (the same mechanical properties in all directions). Parts with large solid areas should usually be hollowed in CAD software to save money and reduce peeling forces however.
We will always wash, post-cure, remove support structures, and gently sand every print, to improve the surface where the supports were. When you receive your print, no further finishing should be needed for the vast majority of applications.
At Printpool we think that fibreglass offers a better cost/benefit ratio than carbon fibre. Reinforced carbon fibre parts are even stronger and stiffer than fibreglass ones, but almost prohibitively expensive.
Although less scalable than SLS 3D Printing, CFR production runs are possible, and we have done this for customers in the past. It really depends on the size and shape of the component.
CFR printing should be considered any time you need a component to have strength and durability that can't be gained any other way. Some customers also choose CFR printing for its exceptional surface finish.
No, its just a little different. Although both powder based processes, MJF parts are a little less accurate, but have the advantage of being naturally waterproof. SLS printing is higher resolution, and better suited to certain types of designs.
Unlike some other technologies, SLS 3D printers produce parts that are entirely solid. Parts are also more isotropic (the same mechanical properties in all directions). Parts with large solid sections should usually be hollowed in CAD software to save money and reduce thermal warping, however.
We will always remove the loose powder, and gently blast your components with unsintered nylon powder, to improve the surface finish. When you receive your print, no further finishing should be needed for the vast majority of applications, but dyeing and smoothing is possible.
Choosing what process to use for each print is critical. Generally 'blockier' parts, with a clear flat surface upon which to build, will be better for CFR, and more organic shapes with smooth curves should be sent for SLS. SLS is also more appropriate for large volumes of the same part.
At Printpool we use a combination of surfacing, solid modelling and sculpting tools from Autodesk, Solidworks and Adobe. The exact tools used vary depending on the task, but we can supply the finished files in just about any format you request.
Lead times for design work vary based on the complexity of the project, and on how busy we are. Generally we can complete simple design projects in a week or two, but complex assemblies or new technology will, of course, take longer.
Of course! 3D printing is our specialism, and so parts we design can always be 3D printed in-house, so that you can have a working prototype of your designs.
Traditional manufacturing processes are so firmly embedded in the minds of designers, that we don't take advantage of all the possibilities that would be open to us without them. We can still 3D print parts that have been designed for other processes of course, which is critical in prototyping, but the most scientifically and mathematically optimised designs require more geometric freedom than these traditional means allow.
Yes, and no. If you want to prototype something that will eventually be injection moulded, for instance, then you should follow all of the design rules for injection moulded components. It would then be our job to find the best 3D printing process to make that part in a representative way. Knowledge of DfAM is still useful though, to understand which process will work best at making that part. Some unimportant features can also be changed to better fit the 3D printing process, so long as that doesn't introduce added difficulty for moulding later on.
We run short courses covering the basics of DfAM. These are split into mini 90 minute sessions covering a 3D printing topic, which are free to attend, and longer, more in depth training, which can be booked on this website.
These terms do seem to have become 'buzzwords' recently, but at the core of the discussion there is some solid science, and some useful concepts. The whole thing is essentially about gathering data about what we make, and using that data to do useful things. Additive manufacturing fits in nicely, as it is an inherently digital process, unlike say, welding.
We can usually provide you with a range of options, including STL, OBJ, and STEP files. If you have a requirement for an unusual file type we will do our best to accommodate you.
We have managed to reverse engineer, and then 3D print replacement parts within a few hours before. Usually projects can be completed within a few days.
We will always need to have access to the original part in order to reproduce it. We will usually use a combination of hand modelling and 3D scanning - both of which require the object to be present in our facility.
3D scanning won't damage the original part, no, unless it is very sensitive to light. If you think that your object is sensitive to light, we can discuss with you in more detail to see what capture methods will be most suitable. We always will return any objects that we have reverse engineered back to you unharmed, at the end of the project.
Our most eco-friendly material is Recycled PLA, which is also compostable using industrial facilities. Bear in mind that additive manufacturing technologies have many other environmental benefits however.
For every 3D printed part that you order with us, we will plant an real tree, typically in mangrove forests in Madagascar. We also offset all of our staffs' carbon footprint using Gold Standard certified carbon offsets, and use recyclable and recycled materials where possible.
Still have more questions? Get in touch and we'll tell you what you need to know.
If you wish to send multiple design files, please put them in a zip folder first! Our website will only accept a single file.
If you require 3D scanning services, please include a picture of the object you need to be scanned.