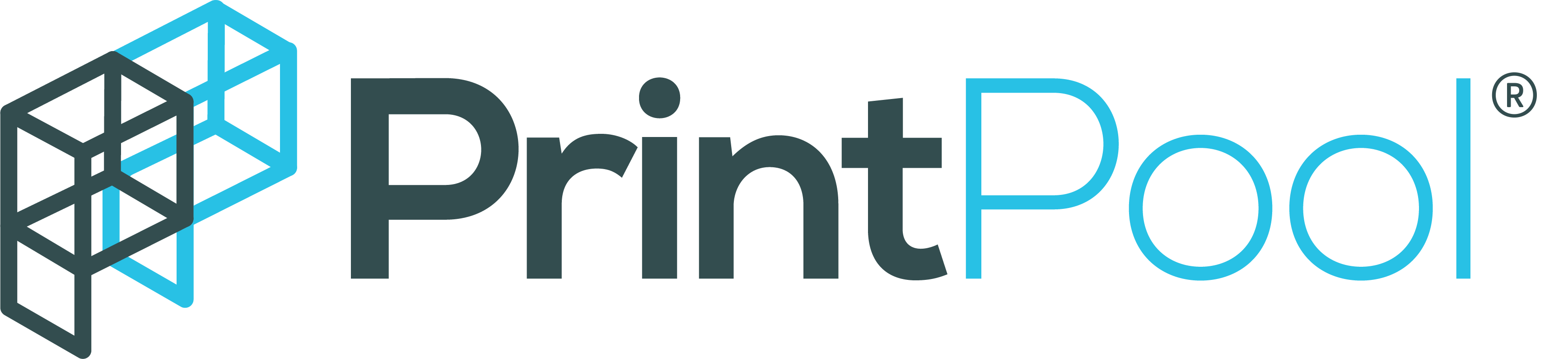
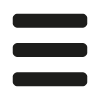
It is a poorly known fact amongst engineers and designers, that in the world of 3d printing, orientation is everything. Without a good understanding of how the direction that a part is printed in affects the result, you will pay more, and receive worse results back in return every time. This article seeks to explain the way this happens, and help you understand how the angle of your parts during additive manufacturing should be considered right from the start.
A quick note: Most of the guides written on this subject cover only the Fused Deposition Modelling (FDM), or extrusion, type of 3D printing. The differences between different part orientations are very obvious with this technology type, but this has led some people to believe that other types of 3D printing are not affected at all. This isn't true. Proper part orientation is important for every type of 3D printing - even (supportless) selective laser sintering (SLS) processes!
Additive manufacturing processes build up parts layer by layer. The direction that these layers are arranged, relative to the shape of the part, is the important factor here. This is because no matter the process (FDM 3D Printing, SLA 3D Printing, SLS 3D Printing etc) the layers of the part give it its defining characteristics.
We often reference the build orientation using cartesian coordinates, as it is a convenient shorthand for an otherwise awkward description. In 3D printing, the z-axis is the direction perpendicular to the layers. Its also generally the direction that gravity acts in, i.e. up and down. The x and y directions are more arbitrary, and can often be swapped without any significant changes in meaning.
The side of the part that faces 'up' (along the z-direction) is what determines the build orientation, as its the cross-section of the part in the x-y plane which forms the shape of each layer.
The material properties of a 3D printed component are influenced hugely by the direction in which it is built, and a typical component is stronger in some directions than others. We call this behaviour anisotropism. A 3D printed part is effectively a laminate, which is to say, its made up of lots of layers pressed together, and it is this quality that makes parts anisotropic. Each type of 3D printing is a little different in this respect, so we'll deal with each type of 3D printing separately.
Due to the way that the layers build on top of each other, the bonds between layers (in the z-direction) are weaker than the bonds in the other directions. This makes FDM printed parts prone to breaking, or delaminating, along the z-direction, when under tensile loading.
It is important when manufacturing functional parts, using this method, to orient the design so that the stresses that it will experience when in use are along the x and y axes.
Resin 3D prints are experience this effect to a much lesser degree than other technologies. This is because when each layer of the part is built, the photopolymerisation reaction that occurs creates a chemical bond between the layers that is almost as strong as those along the layers. SLA parts therefore exhibit nearly completely isotropic behaviour in this regard.
Similar to FDM printing, Selective Laser Sintering parts show slightly reduced strength when under tension in the z-axis. This is due to a weaker bond between sintered layers than adjacent particles of the same layer. The effect is much weaker than with FDM printing however.
To get a better understanding of how a part should be orientated, not just for strength, but for all other considerations, we're going to use an example. We'll consider build a simple shelf bracket, which will experience mechanical stresses when an object is placed onto the shelf.
Orienting a part so that the minimum amount of support material is required is an important consideration. Consider our example part below, which has been set up using an FDM slicer.
Both of these options will produce a part with nearly identical material properties, as they both are orientated with the same axes aligned to the z direction (the fact they are the opposite way around makes no difference). In one of the options however, a huge amount of support material is required, and so the other one may be a better option. The additional support will otherwise increase print time, and waste expensive and polluting material.
If we were to consider making this part using SLA technology, the considerations are similar. The version on the left of the screen will print faster, and waste less material than the one on the right. This isn't the only consideration though.
This one only really affects FDM and CFR prints. Without a stable surface upon which the rest of the part can build, an extrusion based print will almost certainly collapse and fail. As an example, take a look at this possible build orientation.
This build orientation ticks some of the boxes. As all the key surfaces are at 45° to the build plate, meaning that supports won't be needed. This part would also be stronger than in some other possible orientations. The issue here is that the surface touching the buildplate is too small, and so the part is likely to fall over during the print.
The accuracy of 3D printed parts is far from consistent. Although the details of this complex topic are the topic of a different article, we will briefly address the influence that build orientation has on accuracy.
FDM and CFR prints are particular prone to losing accuracy on certain features when they are aligned parallel to the x and y axes. This primarily affects holes, curved features and overhangs. It is best practice to align holes perpendicular to the z-axis wherever possible, to avoid this problem.
Warping is also a big issue in 3D printing, across different 3D print processes and for different reasons. FDM prints can warp due to different rates of cooling between areas of a large part. The way to reduce this effect is to avoid having large flat areas in contact with the build plate - directly contradicting what is required to create a stable base. This is one of the factors that makes DfAM a tricky topic!
SLA prints warp for different reasons. During the printing process, when large areas all undergo the photopolymerisation reaction at the same time, it can be hard to separate this the newly formed surface from the skin of the resin tank. The forces generated, known as 'peeling forces' can lead to warping of the part.
Proper part orientation, to minimise the surface area that gets cured at once, can help. The part on the right of the image is subtly angled so that less of the shape gets built at once. It also has an increased number of supports on the side of the model, which helps to 'anchor' the part to the built platform and so reduce the likelihood of significant warping.
The best orientation for this part will naturally be a compromise between all of these considerations. There are sometimes multiple right answers to the question of the 'correct' orientation, and other times the only thing to do is make a design change or accept that there will be some small flaws in the final part.
In this case, the best orientation that we came up with for FDM/CFR printing was on its side, as shown. This part will built using very little support, and the forces acting on the bracket will be in the x-y plane, meaning that the part should have good strength when it's in use. The lower overall 'z height' will mean that this part prints quickly and accurately.
If we were to make this using FBGR Onyx, using CFR printing, then we could even use continuous fibre in the x-y plane to further strengthen the bracket. This would make for a very strong shelf, as there are no significant forces acting to put the layers in tension, where they could delaminate.
If we wanted to use an SLA resin, then the image above would be the best orientation for the design. Interestingly, angling the part as shown results in a lot of additional support structures being generated. In this case though, that's exactly what we want.
Large flat surfaces are very prone to warping when made using the SLA process. To reduce this effect, we have added extra supports to anchor the part to the bed and resist those forces. This orientation also means that each layer has a relatively small cross-sectional area, reducing peeling forces that could deform the part.
As an added bonus, the exterior faces of the part, which will be visible when the bracket is in place holding up the shelf, have no support structures on them. This will leave a smooth and pristine bracket that keeps our shelf looking its best.
For the SLS orientation, the optimum arrangement would be something like the above image. IN this case, we actually have a large number of different rotations, and the parts are arranged in free-space - unlike other processes. The goal here is to pack a large number of parts into a small volume, making the build more efficient. This is typical with SLS 3D printing and is an important part of reducing waste and optimising manufacturing efficiency, which benefits the environment as well as reducing prices for customers.
Its worth noting that despite the freedom that SLS offers in producing parts with no supports, there are still some results that are followed. In this case, note how none of the parts have been aligned with the axes of the build chamber. Instead, by positioning the parts at jaunty angles, the cross-sectional area of each layer is reduced, and so there is less chance of warping.
Whether you are using 3D printing in-house, and have full control over the build setup, or you outsource to a 3D printing service bureau like Printpool, a good understanding of part orientation is critical. By considering how these factors affect the additive manufacturing process, you will know how your parts are likely to perform during testing.
If you make a prototype using a 3D printed material, did it fail because the design was wrong, or because the layers delaminated due to improper orientation? Could you change the angle of a surface in order to make it print without supports? Would the part you expected to print using an FDM plastic actually print better as an SLA resin?
Asking questions like this will make you a better designer, and help you get more reliable, cheaper 3D prints.