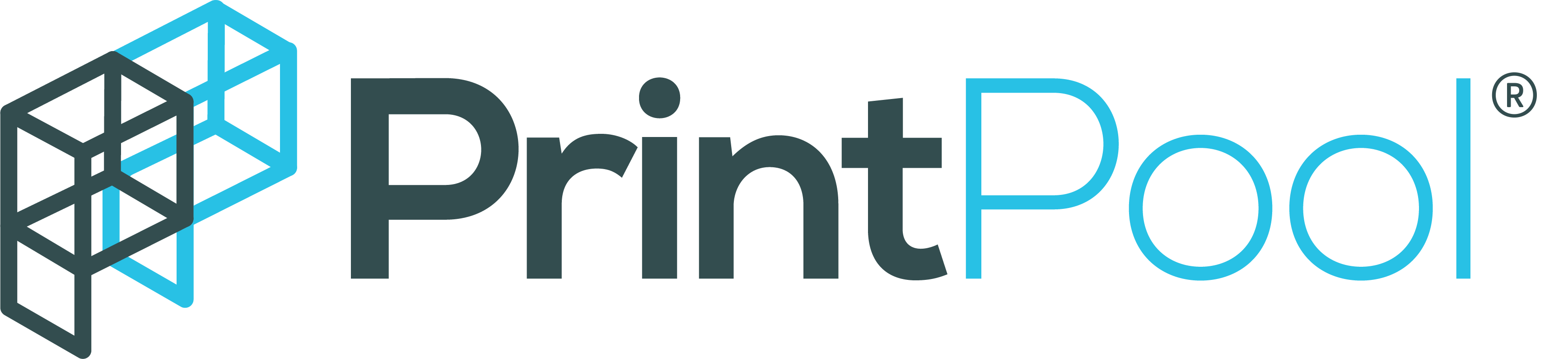
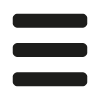
If you work in product design or engineering, you are undoubtedly familiar with 3D printing, and if you're familiar with 3D printing, you probably know that there are lots of different technologies available. The most common, in design studios anyway, are FDM 3D printers, but many businesses now have access to Resin 3D printing too. There is a third major type of 3D printing though, which involves powder.
Powder bed fusion technologies are possibly the most versatile type of 3D printing (or additive manufacturing) as they don't require support structures, offer excellent material properties, and can cost-effectively produce parts in larger quantities than other options. Most studios and workshops don't have this technology in-house however, as it is relatively expensive and requires more attention to health and safety than other types of additive manufacturing.
Luckily, there are 3D printing service bureaus available who can print your designs for you.
The two main types of powder 3D printing technologies, at least for polymers, are Multi Jet Fusion (MJF) and Selective Laser Sintering (SLS). They are very similar in a lot of ways, but do have some key differences, which this article will explore in more detail.
SLS and MJF are very similar. Both processes begin with a layer of fine powder, spread evenly on a flat surface. The powder is heated to just below the melting point of the material being used (normally Nylon 6, Nylon 11, or Nylon 12).
During the SLS 3D printing process, a laser is then used to precisely, and selectively, heat certain areas of the powder bed - which correspond to the cross-section of the component being made. The powder grains in those areas get hot enough to fuse together, while the areas that the laser did not heat remain as a loose powder.
MJF is a little different. During this process, a fusing agent is sprayed onto certain areas of the powder bed - again, corresponding to the cross-section of the design being manufactured. A slightly different detailing agent is sprayed around the perimeter of each area, to keep the edges crisp. An powerful infrared light is then passed over the entire powder bed, and the areas that are coated in the fusing agent heat up, as the IR radiation is absorbed. The areas that aren't coated in the binding agent, do not heat up, and remain as a loose powder.
In both cases, the next layer begins when a fresh layer of powder is evenly spread over the build surface, and the process repeats. In both cases, support materials are not required, as the unfused powder supports the parts, and in both cases, the powder material must be left to slowly cool down once the process is complete - to prevent parts from warping.
By far the most common material for both technology types is Nylon 12, sometimes known as Polyamide 12. This is an excellent general use material that has a good balance of strength, heat resistance and easy processing.
Nylon 11, Glass-reinforced Nylon 12, and various elastomeric Thermoplastic Polyurethanes (TPUs) are also commonly used with both SLS and MJF technologies. The similarity of the available materials is no coincidence, and is largely due to the similarities of the two processes.
One of the major advantages that MJF has, is the relatively lower price for some, but not all, parts. Parts that are very small, or parts that are particularly dense, are often cheaper using SLS 3D printing, but some other parts will be cheaper using MJF.
The difference can vary a lot in absolute terms, and in particular with the exact part geometry. The differences in price are mainly down to the price of the binding agent in MJF, and the different refresh rates, which determine the degree of powder wastage, as well as the absolute cost of the machine.
Recently, new entrants to the SLS market have brought prices down significantly in comparison to MJF. Formlabs, SinterIt, and Sintratec and WeMatter have all released models for under £100,000 in recent years, beating out HP multi jet fusion hardware in terms of price.
Even for those who intend to outsource their 3D printing requirements, the upfront cost of the machine still matters, as service providers will of course pass on a percentage of this cost to their customers per component.
Quality is a difficult trait to define precisely, but the following categories are usually good indicators for most additive manufacturing technology.
Both the selective laser sintering and multi jet fusion process have similar resolution. Although HP claim that MJF parts have a minimum feature size of 0.5mm, we have found this is often not the case, and the minimum part size is essentially the same as SLS. Small holes can be slightly rounder using MJF technology than SLS however.
The mechanical properties of a given material, when made using SLS or MJF, are very similar. MJF parts are slightly more isotropic than SLS parts however, meaning that orientation has a smaller effect, and they have more consistent mechanical properties.
The appearance, and surface finish of parts printed using SLS technology are very similar to those printed using MJF. Both produce parts with a slightly textured, powdery finish, not unlike sandstone (but with a very fine grain). The surface finish can be improved by polishing, shot peening, or vapour polishing, to achieve smooth surfaces, and both types of material can be dyed and painted.
MJF powder is grey, and so are MJF parts, whereas SLS parts can be either white or grey depending on the machine. White parts are easier to dye different colours, but require a higher power laser, as dark materials absorb radiation more easily than lighter ones.
MJF parts are prone to showing visible scratches and scuffs, which are less obvious on SLS parts.
We have consistently found that SLS has very high dimensional accuracy, whereas MJF systems are more variable. This is mainly due to warping effects, which MJF parts are very prone to. Parts that are very flat, or have a very high slenderness ratio, are likely to warp when made using any powder bed technologies, but the effect will be more noticeable if they are made MJF.
Relatively small, well designed parts, will have similar accuracy on both systems.
The build volume for SLS 3D printing is very variable; It can be anywhere from 110mm x 160mm x 130mm to 700mm x 380mm x 580mm, or above, depending on the make of the machine. MJF is a proprietary process however, owned by Hewlett Packard, and so the build volume is 380mm x 284mm x 380 mm.
To conclude, both SLS printing and MJF printing are excellent, and similar, 3D printing technologies that use plastic powder to manufacture high performance parts.
What differences do exist, are fairly slight, and often the choice between the two technologies comes down to other factors, such as availability and turnaround time, rather than any significant differences in the core powder bed fusion technology.
When large parts with tight tolerances are needed, SLS machines often have a slight edge. MJF tends to have a price advantage over SLS in some circumstances, but this is only usually noticeable when service bureaus offer both technologies, as the price variation between bureaus is even more noticeable still.