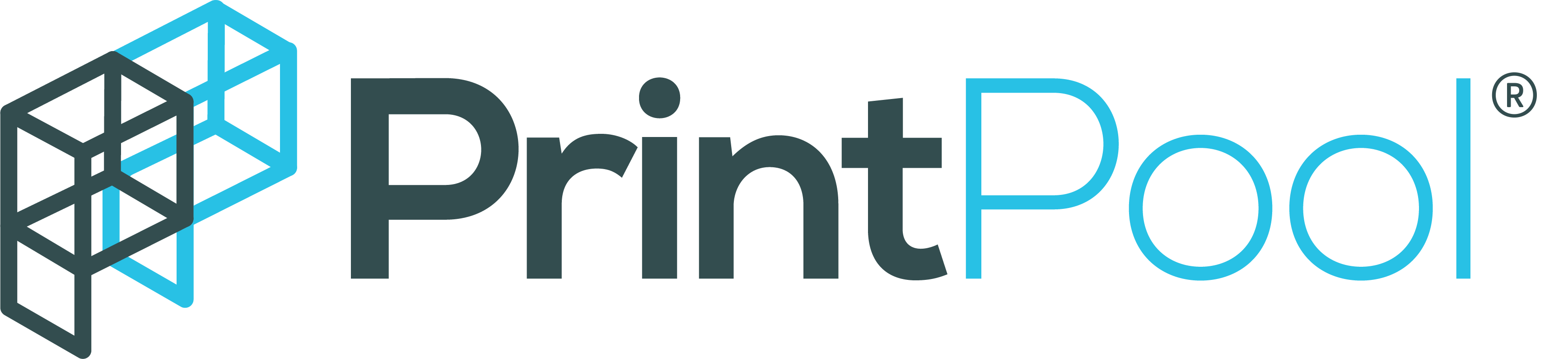
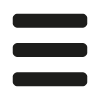
Those of you who have been working in engineering or product design for some time will know how important design for manufacture (DFM) is. This is because the way an object will be manufactured changes everything about what options are available to you when you are designing it.
Some features that you may wish to include in your design are simply not compatible with certain manufacturing processes. This is why designers will often refer to design guides that are specific to the manufacturing process they wish to use, to make sure the size and form of the various features they need are within the correct limits.
Some processes lend themselves well to making large volumes of parts, and some don't. For example, injection moulding is perfect for the mass production of simple components. Other processes are known for producing very high strength parts. The aerospace industry often uses CNC machining to produce very strong, accurate parts from performance alloys, for example.
Different processes also have different costs. Injection moulding has a high setup cost, which reflects the price of machining steel tooling, but a very low unit cost once that tooling has been made. Conversely, additive manufacturing methods have a high unit cost, but no setup cost at all. This makes 3D printing a good option for small batches of parts, but larger volumes are often more economical made using injection moulding.
There are three categories of manufacturing process. They are subtractive manufacturing, formative manufacturing, and additive manufacturing. The first two of these are generally referred to as traditional manufacturing techniques, while additive manufacturing (3D printing) is usually given its own category, or grouped in with other advanced manufacturing technologies.
Most manufacturing processes are subtractive. Starting with a big block of material, various cutting tools are used to remove material that isn't wanted, until only the useful bit remains. Milling, drilling, turning, and grinding are all common subtractive manufacturing techniques.
All else being equal, these techniques are often very precise, but each new feature adds cost and time to the process. Subtractively manufactured components are generally very strong, as they are made from a billet of solid material.
Formative manufacturing processes involve changing the shape of a given volume of material so that it becomes useful. Usually this is done by heating the material until molten, and then using a mould to give it a new shape, before it cools and solidifies. Sand casting, die casting, and injection moulding are examples of this, and so are most forging processes.
Generally parts made using formative means have restrictions on minimum and maximum wall thickness. This is so that molten material can flow easily throughout the mould, and so that no sinking or warping occurs when the part is cooling.
Additive manufacturing is the final family, and includes seven major categories of 3D printing technology. The crucial differentiating factor is that a part is created layer by layer, starting from nothing, and 'adding' material.
Most additive manufacturing methods excel at producing complex designs, including lattice structures, and complex surfaces – but are usually not very cost effective when producing large, simple designs.
There are some voices in the industry that seem to think that additive manufacturing is the solution to every manufacturing challenge in the world – and they are wrong.
Injection moulding produces parts that are of very high quality, and high strength. It's an incredibly effective process, that has been refined over decades to become a mainstay of modern manufacturing. Injection moulding is the perfect mass production method to produce thousands of fairly simple, thin walled components, that are all identical.
Machining is another traditional process that is irreplaceable for the right use-case. The best time to use this type of manufacturing is when you need small to medium scale production of high precision, strong parts. The tolerances that are achievable using modern machining methods are incredible, so long as you are willing to pay for the additional accuracy. Machined parts offer engineers a good amount of design freedom. Thick wall sections pose no problem, and will be at 100% density, unlike with most additive processes. This opens up possibilities for extremely high-performing parts.
None of this means that additive manufacturing doesn't have a strong value proposition, and a growing number of applications make it the production method of choice in many scenarios. This is because additive manufacturing succeeds where traditional methods begin to fail.
3D printing only makes sense for certain design and manufacturing challenges. In general, these scenarios are ones where traditional manufacturing tools perform poorly. Put simply, 3D printing is great at doing three things.
The first is making small numbers of parts in a fast and cost-effective way. This is why 3D printing was sometimes referred to as rapid prototyping, particularly a few years ago. Prototyping is a real strength of additive manufacturing techniques, although this is something that the 3D printing industry has been keen to downplay in recent years. No, prototyping isn't all that additive tools can do. Yes, it still does this really, really well.
The second is making complex things. Lattice structures, complex surfaces, generatively-designed parts and parts with complicated internal voids and channels can all be made easily using 3D printing. These are also all things that are difficult or impossible to make using conventional methods. Intricate designs for the medical industry, and jewellery applications, are also really strong use-cases.
Finally, 3D printing is great for mass customisation. This is where a part or product is manufactured slightly differently every time, to match the customer's or end-users needs. This could be an earphone that is perfectly matched to the size and shape of the listener's ear, or art pieces that are all slightly different, and therefore one-of-a-kind. Although the designs are different, their similarities means that they can still be manufactured using additive mass-production, and therefore the same savings can be made for large orders. Designs can also be changed halfway through a production run of components without penalty.
Lets look more closely at some examples where 3D printing technology can outperform injection moulding.
Without further preamble, lets look at seven examples where 3D printing might be more effective than traditional manufacturing when making plastic components in high volumes.
The price of injection moulding varies a lot, and one of the most important influences is how many moving pieces the mould requires. A simple, two piece mould will be much cheaper than a multi part mould with several shut-offs and sliding cores.
The complexity of the part that you need to make directly corresponds to the complexity of the mould required, which in turn affects the cost. All else being equal therefore, a complex design means a high price, when it comes to processes such as injection moulding.
Additive manufacturing offers the ability to get this complexity for free. Generally AM parts are priced by volume of material used, and time taken to build. Counterintuitively, this means that complex parts are often cheaper than simple ones (as they need less material).
Does a few hundred components count as mass production? For some industries, it can. A few hundred medium complexity parts is very often cheapest when made using additive manufacturing methods.
The high setup costs of the injection moulding process can make small to medium volume production uneconomical, and machining is very wasteful for this quantity of parts. Additive technologies can fill the gap.
Mass production has many benefits, and will allow you to produce many thousands of identical parts with a low unit cost. However, what if your design changes?
There are lots of reasons that this might happen. Perhaps you made a small mistake, and a feature is just slightly smaller than it should be. Now when your product is assembled, your parts don't fit together quite right. Even the most rigorous prototyping processes and systems can occasionally let an error through.
It may be that new standards come in, or you want to sell in a new market, and this demands a small change to your design, or perhaps you get feedback from customers that a particular feature is undesirable, and you need to edit one of the components.
In all these cases, it will be an expensive problem when mass producing parts with injection moulding. If you are 3D printing your parts however, it probably won't cost you a penny to tweak your design part way through a production run.
Additive technologies excel at producing complex shapes, as the cost and cycle time is independent of the number of features. Instead, the cost of additive components is more closely linked to their size, and therefore the amount of material that is needed.
This means that relatively small plastic parts, which are highly complex, are often a perfect fit for cost effective mass production using additive means. The cost, delivery schedule, and quality can often be far superior to plastic injection moulding methods that are more commonly used for mass manufacturing or high volume production.
The setup for injection moulding requires a steel or aluminium tool to be made, and this takes time. It is expensive, and slow. Turnaround times of several weeks are considered very fast for this process, and complex multipart moulds can take your supply chain months to manufacture.
Additive manufacturing has no such limitations. The setup time for both mass production and low volume production is exactly the same, and can be only a matter of minutes. Printpool has previously launched the production of hundreds of components only a few minutes after receipt of a purchase order, and been able to dispatch them next day.
If you need parts quickly, particularly if your designs are physically quite small – 3D printing methods will likely be far faster. This can make the process highly cost-effective even when the unit costs are higher, as a slow production schedule can be very expensive and inefficient.
Due to the complicated setup process inherent in injection moulding, it is almost always most efficient to mass produce parts in one big batch. High volume production runs make the most economic sense to minimise setup fees.
This does create a problem however, when thousands of components arrive in your facility, and there is nowhere to put them. You will have to pay for warehousing, and the reality is that most of them will sit on the shelf for a long time, until staff are available to assemble them, and demand starts to catch up with supply.
3D printing methods have no setup costs. This means it is actually often cheaper, as well as more convenient, to have regular deliveries of parts on demand. No warehousing required. Just the parts you need, when you need them, on a flexible schedule that matches the demand for your products over time.
We all want to believe that the products we design will be instant bestsellers, but in reality, the market is a fickle beast. Your designs may sell in the exact volumes you expect, or your estimates may be wildly over or under the actual figures.
If you have opted for traditional tooling, inaccurate estimates like this may cost you tens of thousands of pounds if you have overestimated demand. Tooling is expensive, and you really rely on large volumes to bring down the effective unit cost.
Underestimating can cause other issues, particularly if you have opted for short-run aluminium tooling, when you should have ordered steel. You may also end up with new customers experiencing a huge waiting time, and lose out as they gradually drop off the waitlist and explore other options.
Once again, 3D printing solves these problems – for the right design. As the 3D printing unit price is relatively static, you can order smaller quantities at first, and increase over time as required without a big penalty.
If you have a design project where you feel these scenarios might apply, get in touch today. We'll take a look at your designs and give you some advice on whether looking at high volume 3D printing would be appropriate for your project, or not. Reach out through the website, or email enquiries@printpool.co.uk .