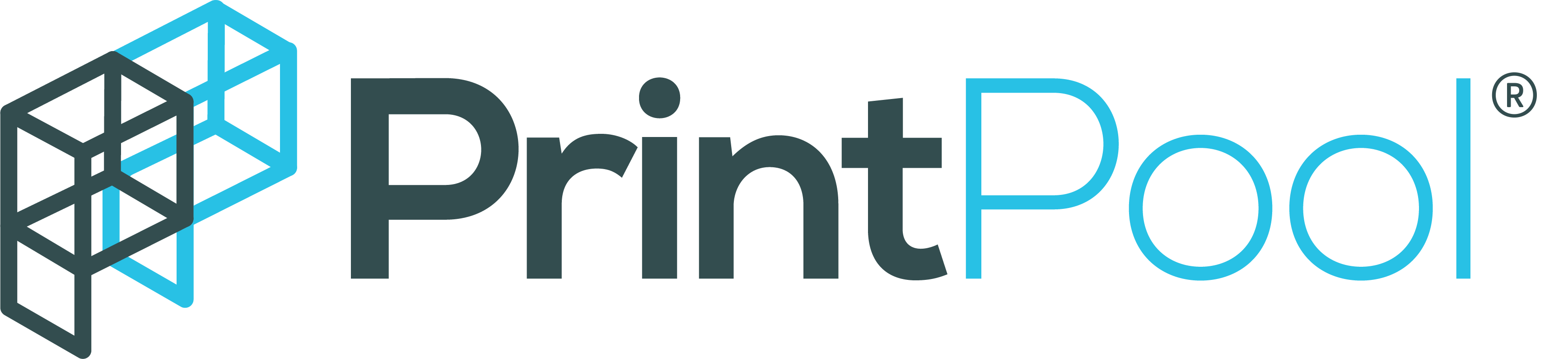
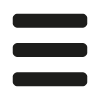
When UltiMaker released the new UltiMaker S7 earlier this year, I was far from convinced. In fact, when I posted my initial thoughts on the new machine on LinkedIn, I was really quite critical. It seemed to me that UltiMaker had taken the admittedly fabulous S5 3D printer, sprinkled some glitter over it, and rereleased it with a new name to get some easy sales. Around 10,000 people saw my post, and a lot of the comments were broadly in agreement with me.
Shortly after I posted though, Lars Bognar reached out to me. Lars worked for Ford for a little over six years, and won multiple awards for his work as an additive manufacturing research engineer. He is now a product manager for UltiMaker, and is responsible for ensuring that customer needs are accurately captured, and good solutions are developed, before they make their way into new UltiMaker products.
Lars wanted to chat with me about the UltiMaker S7, and explain how it came to be, as well as justifying some of the decisions the team made in its development. So we set a date, and I met him virtually to get a better idea of what the S7 is all about.
I was a little wary, imagining that perhaps Lars may be frustrated with me for my criticisms of the new machine. This fear was unfounded however, and I learned that my initial criticisms were nothing Lars hadn't already heard.
"We got some negative comments, especially from our current customers. It's funny, because actually they are complaining, but in the same sentence they are telling us how good the machines are. For example there was one comment, 'I've been using my UltiMaker 2+ Connect for five years now. No complaints, and its running perfectly. Why should I now buy an S7?' This could be perceived as a negative comment but his old 3D printer has been running for five years and he's thinking about another one!"
This is a very fair point. UltiMaker have a well justified reputation for consistency, and reliability which is hard to beat across the industry. This reliability is a huge factor for us, running a bureau service, as a broken 3D printer can quickly disrupt print schedules.
My own frustrations however, were centred around weak differentiation from the previous model. It seemed to me that this was not enough change to warrant a new release. I asked Lars if UltiMaker had considered simply branding this 3D printer as a variation of the S5.
"There are arguments against and in favour of that. We thought if we just called it the S5+, or S5 Pro, then that would lead to more of these comments, saying 'Its nothing new' or 'Its just an S5', and that would lead to more comments - maybe disappointment. We believe that the improvements are big enough, and we consider it a new machine."
So, with that in mind, what does the UltiMaker S7 have to offer?
The UltiMaker s7 certainly has some features that the S5 doesn't. For a start, the air manager, which was an optional accessory for the UltiMaker S5, is now a integrated into the body of the machine, to give a fully enclosed build chamber.
An enclosed build volume has many advantages, such as making it easier to print tricky materials like ABS. Ultrafine particles, which may pose health risks, are also filtered effectively by the integrated air manager. A more consistent temperature in the build environment boosts print quality, and reduces the chance of parts warping because of a cool draught.
Lars explained however, that the decision to build the air manager into the frame of the S7 was mainly due to customer demand for what was previously an accessory.
"From a business standpoint, we had the majority of S5 customers buying the air manager anyway. Around 80% of customers were using the air manager with the S5. It also gave us a possibility with a new camera angle. There was a complaint that you could only see the first layer. With this bigger housing - the angle from the camera is now better."
Admittedly, the camera did give a pretty poor view on the S5, so this is a welcome improvement, if not a critical one. The camera has also been upgraded to 1080p, which is nice, I suppose.
"The machine is also much, much quieter with this new setup, so you can barely hear the machine printing. which is also, compared to our competitors, a big plus if you want to run the machine in an office."
My company, Printpool, is a 3D printing service bureau, so the machine making less noise isn't a big factor for us. We have a more industrial setup. That being said, one of the things customers loved about the award winning UltiMaker S5 was its ease of setup and easy printing - perfect for an office environment. Many studios have an UltiMaker 3D printer in the same room as the design team, so reduced noise is certainly a plus for many users.
Another new feature is the flexible PEI coated build plate, which offers reliable print adhesion, but with faster print removal speeds and ease of use. Previous UltiMaker 3D printers have used a glass build plate, which offers a perfectly flat surface (good) but can make it difficult to remove certain parts once the print has finished.
Lars had this to say:
"The flex plate is also a game-changer from a UX perspective. We worked closely together with the supplier, to really define the surface roughness, to within very very tight margins. It was very very difficult to develop that. The flex plate will be expensive compared to competitors, but its worth it. The adhesion is so much better, the release is flawless. We think this is the best flex plate out there."
This is a heavily shortened version of Lars' full thoughts on the new build plate. His passion for the world of additive manufacturing really shone through here, and by the time he had finished, I was as convinced as he was. I'm very excited to try it out.
We've never had any issues with the automatic bed levelling function on the UltiMaker S5. Honestly, it has always worked pretty much flawlessly, and has been a really useful feature. Not everyone has had the same experience however. Multiple people commented on my LinkedIn post explaining the problems they had experienced getting the UltiMaker S5 3D printer to level properly.
Lar's explained that 1 in 6 failed prints was down to levelling issues, and so the new inductive probing strategy should make a big difference, as it is significantly more accurate.
"Especially from a reliability standpoint, the inductive sensor and new probing algorithm is much more precise and much more reliable, so there will be way fewer first layer issues."
Experienced 3D print operators know that reliable first layer adhesion is a key factor in print success, and will often wait and watch the build plate while the first layer is built. If this feature is as good as UltiMaker claim, I expect more companies may begin to trust remote printing.
The UltiMaker S7 also features a few other minor changes. The machine now has a single glass door, to replace the double door on the S5. This is because the space in between the two panes of glass was previously prone to letting a small draught through, which could disturb the temperature of the build environment enough to cause warping issues.
The machine offers backwards compatibility with UltiMaker S5 print jobs, and also the material station, which offers automatic humidity control and material handling for both the S5 and S7 models. The material station is a useful addition to both machines, and really brings the UltiMaker S7 to a new level.
The UltiMaker S7 also has an anti-flood sensor. We experienced a flooded printhead on an UltiMaker S5 for the first time recently, which means it had filled up with molten plastic, and then cooled. This is incredibly difficult to fix, and it took us several hours of repairs to extract all the plastic without damaging any components. The anti-flood sensor is therefore an extremely welcome addition.
Finally, we spoke about a new competitor on the market. Bambu Lab appeared on the scene last year, and have near instantly won over a huge number of fans, mainly due to incredibly fast 3D printing speeds and overall value on the Bambu Lab X1 - their debut machine. This machine also has a material station, and early reviews for all their hardware seem to be very positive.
I asked Lars what he thought.
"We're focusing on reliability, we're focusing on the ecosystem, materials and software. That is where we have the biggest advantage against our competitors. The whole ecosystem just works. Do you want to have fancy new technology? Or do you want to have a reliable printer that does what it needs to do. These machines need to prove that they are still working in five years."
In my original LinkedIn post, I said the following:
"The price hasn't been made public yet (as far as I'm aware) but if it is more than the cost of the S5 + Air Manager combined then it seems like a poor deal to me."
When Lars and I spoke back in late January, the pricing for the new machine had still not yet been released. It is now available however,
I think I was more than a little harsh back then. The UltiMaker S7 is retailing at only a small premium to the combined price of the S5 and its air manager (in the UK), so you would be crazy not to go for the S7 if you're buying a new UltiMaker. The novel features that have been developed may not be radical, but they are steady, genuine improvements over the UltiMaker S7's predecessor, which we shouldn't forget, was absolutely outstanding.
I still think the S7 is a little too close to the S5 to claim it is a completely new 3D printer though. Personally, I would have received this better as an UltiMaker S5 Pro, for example, but I can certainly see Lars' point that others may not share this view.
At Printpool, we love UltiMaker machines. They are workhorses, with exceptional part quality, require next to no downtime for maintenance. They have an open filament system, which is hugely helpful when facing varied customer requests, and the print success rate is near perfect. UltiMaker materials are also excellent, and print flawlessly on the corresponding hardware.
So to sum up, we won't be trading in all our UltiMaker S5's for the newer model anytime soon.
But, we're definitely going to buy an S7 next.