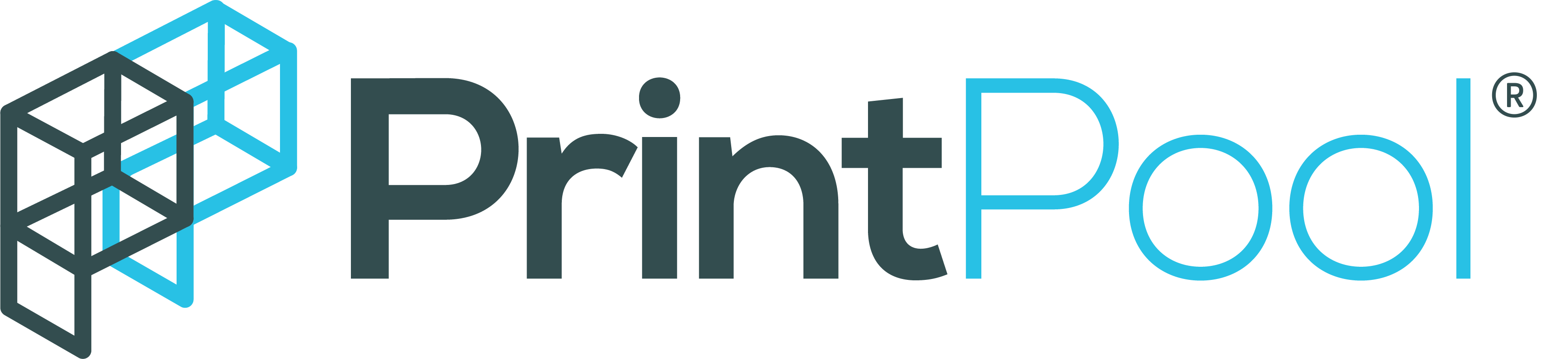
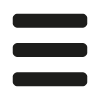
Before we can discuss design for resin 3D printing in depth, its useful to understand a bit more about the process. SLA 3D printing was actually the first type of 3D printing to be discovered - all the way back in 1984. The letters SLA stand for StereoLithography Apparatus, as named by Chuck Hull, who also invented the process.
In most forms of SLA, a laser is shone onto a pool of liquid resin, which contains photopolymers. Photopolymers are simply polymers that react with light, resulting in structural changes at a molecular level. When laser light hits the liquid resin, it hardens (or cures) changing it from a liquid to a solid. More resin is then allowed to flow over the newly solid layer, and the 3D printing process repeats, so that a part is built up, layer by layer.
SLA parts typically have a very smooth surface finish, and build on a scaffold of supports, that has to be removed by hand. SLA resins for 3D printing come in a number of different formulations, that can have a wide variety of different properties, from very tough and flexible resins, to stiffer and harder resins, and even specialist options, like dental resins.
The UV laser only partially cures the material. After the SLA print process has finished, the models must be post-processed, and until this happens, they are considered to be in a 'green' state. The material properties of these 'green parts' are very poor - they are delicate and potentially irritating to the skin also.
First, parts must be washed in Isopropyl Alcohol (IPA). This helps to prevent uncured resin from settling in areas that it shouldn't. Once cleaned, and dried, parts are placed in a UV oven, to allow the photosensitive resin to fully and completely cure. The layers chemically bond to one another at this point, and the full mechanical properties of each material is realised.
After post-processing, parts are allowed to cool, and then are ready for support removal.
The photopolymer resin layer doesn't necessarily need to be cured with a UV laser. Other light sources, including light from the visible part of the spectrum, can also be used. In this case, a projector or LCD screen is generally used, as they are cheap, highly accurate and easy to source. This variation of the technology is known as DLP (Digital Light Processing) 3D printing, or MSLA (Masked Stereolithography) respectively.
SLA and DLP/MSLA printing are very similar. Both involve the use of chemical photopolymers and a light source, and build parts that have very similar properties and a near identical appearance. There are a few minor differences though. We've written more extensively about these in this article, which compares the two types.
When a layer finishes building on an inverted SLA 3D printer, it is chemically bonded to the bottom of the build vat. For the next layer to begin building, this bond must be broken, allowing fresh resin to coat the bottom of the vat. Usually this bond is broken by moving the build plate up and away, briefly, before dropping it back down into the resin.
Breaking this bond, between the build vat and the newly printed layer, is known as peeling. The peeling forces, required to do this, can distort the part, roughen the surface finish, and even break or rip the build vat in some cases.
The magnitude of the peeling forces present in SLA prints are proportional to the cross-sectional surface area of each layer. It is good practice when designing parts for SLA 3D printing therefore, to reduce this cross-sectional area as much as possible, either with design decisions, or by reorienting the part relative to the build vat/platform. We talk more about orientation in the 3D printing process in other articles.
Even within the 'family' not every SLA printer works in precisely the same way. In 2019, the Formlabs Form 3 was released, which uses a slightly different variant of SLA technology, called Low-Force Stereolithography.
Previously, there were two big issues with SLA printing. The first was that when the laser beam was aimed at the very corners of the build platform, the laser beam 'spot' became distorted due to the angle, into more of an oval. This affected the resolution in a serious way on larger parts. This issue was addressed by using a series of lenses and mirrors to ensure the laser light hits the surface of the resin tank in a perfectly perpendicular fashion.
The second issue, was that where parts had large cross-sectional surface areas, there were significant peel forces on parts. As described above, this leads to distortion and reduced surface finish, as well as a limit on the build volume of inverted SLA printers. Formlabs addressed this issue by creating a flexible film on the bottom of their Form 3 resin tanks, and a specialised laser module, to gently stretch and pull the flexible film away from 3D printed parts, resulting in much lower peel forces.
At Printpool we use the Low-Force SLA printing process exclusively, using the Formlabs hardware ecosystem.
Unlike many other types of additive manufacturing, SLA materials are largely isotropic once fully cured. Layers are chemically (covalently) bonded to one another during the SLA printing process, and so most SLA printed parts will have the same mechanical properties in each direction.
As a mechanical engineer, industrial designer, or product designer, here is everything you need to know about designing outstanding components and assemblies for SLA printing.
SLA printed parts require support structures in most cases. Like FDM and CFR 3D printing, the SLA process can't be used to build on 'empty space'. It is possible to create designs that are self-supporting, however generally this is more challenging to achieve than when using FDM 3D printing.
SLA support structures are almost always removed manually. This can be quite challenging when working on certain designs. Usually flush-cutters are used to carefully clip the supports where they contact the model, and then the resulting bump is manually sanded down to a smooth surface finish. On hard to access areas of the design, this may not be possible, and so care must be taken to either orient the part so that these areas don't require support at all, or so that these areas are removed from the design entirely.
You should remember that supports will be required when your parts are built using SLA 3D printing. By keeping this in mind during the design stage, you can ensure that they will be easily removable, and that the surfaces where they are in contact with the part surface will be accessible for sanding, for the best possible surface quality.
Directly 3D printing threads is only possible using SLA resins for sizes larger than M4, and we don't recommend it for anything more than a cosmetic feature. For functional parts, requiring a firm threaded connection, the best approach is to use a 'screw-to-expand' insert, which can be added to the part before final curing in a UV oven.
For designs where this isn't possible, the next best option is a captive nut/bolt. This requires a little more design knowhow, but has the benefit that the design can be reused with other materials, and will always work.
Bonding SLA printed components to each other directly is also a good alternative to adding threaded connections. There are a variety of different adhesives that work well on SLA resin parts, but we usually use either cyanoacrylates (superglues) or epoxy-based options. Bear in mind that most adhesives won't work on uncured resin, so its important to make sure that parts are fully cured before bonding.
Designers are sometimes taught to avoid adding unnecessary fillets, chamfers, curves and details into their designs so that the cost of their designs can be kept down. This does not apply when designing for additive manufacturing. One of the most common ways that SLA parts fail is brittle fractures, particularly when using less durable resins, and as sharp edges act as stress-raisers, they make this more likely.
Sharp edges, in particular those around highly stresses areas, should be avoided as much as possible therefore, and replaced with either chamfers or fillets. This will reduce the tendency of the design to fail by cracking or shattering.
We've discussed before how size is critical, especially when it comes to the price of 3D printing. This is no different with SLA resins. In fact, as its more challenging to pack multiple models onto an SLA printer, the size of your model can have an even bigger impact.
Unlike some other processes, it is also possible to manufacture incredibly small components using SLA 3D printing processes, making it a good option for the manufacture of scale models.
SLA resin parts are known for their excellent surface finish and the fine detail. Achieving excellent print quality is actually more complex than some designers may realise however, and creating smooth surfaces, that are key for visual models, can be a challenge in some instances.
As support scaffolds are required for most sla printed parts, there will always be one 'side' of an SLA print that has a poorer surface finish. This is because supports need to be mechanically removed. Supports must be made from the same material as the model, so the dissolvable support structures that are sometimes used in other types of additive manufacturing are not an option.
Once support structures have been removed, small marks can be left behind. Where these marks are made by material protruding from the surface, the area can be sanded down, and a good surface can be achieved. Sometimes however, the marks are made by concave sections, where the removal of the supports has caused a little bit of extra material to be removed from the surface. These marks are harder to remove, requiring either filling the holes, or sanding the entire surface down, to remove.
It is good practice therefore to ensure that as few supports are needed as possible, and that they need not be placed in areas of the model that are critical to the overall appearance of the model. Access is also required to remove the supports, so large, internal cavities may fill with support that can't be removed through a small opening, for instance.
Parts can be sanded and polished with mineral oil for a better finish. At Printpool, we have sound that this is the best way to hide the appearance of support marks, and we routinely use mineral oil for finishing SLA parts.
The SLA printing process is generally highly accurate, but the primary cause of tolerance issues is when parts warp. This happens for two reasons.
The first, is the SLA additive manufacturing process itself. As each layer bonds to the one below, it 'tightens' or shrinks slightly, as new chemical bonds are formed. Normally this makes an imperceptible change to the size, but when large areas of resin are cured at once, this can add up to a noticeable effect.
The second reason is during the post-curing phase. The UV oven used to finish the curing process heats parts to between 50°C and 80°C. Sometimes when parts are cooling afterwards, the thicker areas of a design can cool more slowly than thinner areas. This causes stresses due to the different degrees of thermal expansion across a part.
The cure for both of these issues is the same. Avoid designing in large areas of solid material where possible. Try to keep wall thickness as constant as possible, and where they must change, try to keep the transition between different areas as gradual as possible.
Large, flat pieces are particularly prone to issues. We will usually advise alternative additive processes to manufacture these designs, or use additional support structures to resist the stresses that could lead to warping.
Large solid areas should be hollowed where possible to resist warping. This will also save money, as less material will be needed to manufacture your design. When hollowing a part, drainage holes should be added to allow uncured resin to escape from the void. These should be a minimum of 8mm in diameter, and we recommend placing the hole in an unobtrusive spot where possible.
A manufacturability issue unique to the inverted SLA 3D printing process is cupping. SLA machines print your part from the bottom to the top, and sometimes enclosed volumes of solid material can form, with an opening facing the resin vat. This is known as a 'cup'. When the part is lowered into the resin after each layer, air gets trapped in this cup, and the increased air pressure when the part contacts the resin can cause a blowout - where the side of your part essentially explodes outwards, damaging it beyond repair. Sometimes the resin vat itself can also be damaged - spilling resin onto the laser module.
Cups can usually be avoided by reorienting the part, so that the cup no longer forms. Adding drainage holes, sometimes called vent holes when referring to cups, can also help, by allowing air pressure to equalise.
Designing for the SLA 3D printing process from the start is important, especially when producing parts that are more than just prototypes.
We advise the following general order for designing parts to be made using SLA 3D printing. Feel free to share this with others, or to use it to explain design considerations to colleagues.
Note that when producing prototypes, that will eventually be made using other manufacturing processes, you can skip steps 3 to 6, as you should design your part for those processes, instead of 3D printing methods.
Without a good understanding of exactly what your part must do, it is impossible to design an effective component. Most times the clearer you are at this stage, and the better defined the use case is, the better the final part will be.
There are a wide variety of different SLA 3D printing materials available. Good 3D printing providers will work with you to identify the best materials for your application, and the very best (like us) may even buy in materials specially, when required, to meet your needs.
Sometimes it may turn out that the best material for you is actually an FDM 3D printing filament, or SLS powder. That's ok! It's better to know that at this stage than when you've already committed to designing for resin 3D printing.
Traditional manufacturing has influences engineering designers a lot. You learn early on to produce cost effective components by making as few cuts into a solid billet of material as possible. This keeps manufacturing costs down, but only when using traditional manufacturing.
That is exactly what shouldn't be done here. The best way to design for an additive manufacturing process is to focus on designing in functionality first, and then add material slowly and reluctantly afterwards.
Using the example of a hole, using CAD model the correct size and depth. Only add the amount of material around the hole needed to make it practical and strong enough to work (maybe 5-15mm, depending on material). Leave this feature floating in free space as a separate body, and then move onto the next one - perhaps a complex surface that interfaces with the user's hand, or a battery housing. Again, use the minimum of material.
At this point you'll have a number of free floating bodies. The goal is now to connect them into a single component, using as little material as possible. For SLA 3D printing, we often use generative design techniques at this point.
You'll probably have a blocky part now, that's just about in one piece. Further refine your design, by removing any material that doesn't fulfil a specific purpose or function.
By this point in the design process you should have a good idea of what orientation is best for your design. Look at the angles between surfaces and the location of key features. Think about what direction forces are likely to act, and how the part should be built with that in mind. Remember that hole orientation is particularly important.
Go back over your design with this orientation in mind. This can be an iterative process, and you may find that you change your mind about the print orientation as you go. Eventually however, you'll have a part that is optimised for a particular print direction, that prints with less support material, and is strong enough for use.
Some final design changes may be necessary to ensure that the specific printer you use, or your service provider uses, is happy with the size of all your features. Once this is complete you can export your design for additive manufacturing.
These guidelines are the ones we use to evaluate the feasibility of resin 3D printing designs. Each service provider will have their own versions of these guidelines, but most are fairly similar.
The maximum part size we can print in one piece is currently 145mm × 145mm × 185 mm. Other 3D printing providers, and machines, will vary. More expensive machines generally have a higher print speed which can make a big difference on large jobs.
We recommend a minimum hole diameter of 0.8mm if orientated vertically, and 1.2mm if orientated horizontally. When aligned along a horizontal axis, holes can be printed without supports when up to 4mm in diameter. It is more difficult to remove support material from blind holes, so bear this in mind when designing.
We recommend a maximum overhang angle of 60 degrees to print without supports. Perpendicular overhangs will generally still be printable, but will have a significantly poorer surface finish.
We have a suggested minimum wall thickness of 1.5mm for most resin 3D printing, on vertical walls. Horizontal wall thickness, where supports will be required, should be at least 3.0mm thick. Where a vertical wall connects to many other walls, you may be able to get away with slightly thinner designs, as each one is better supported.
Embossed writing or logos should be a minimum of 0.6mm thick, with at least 0.4mm of depth (or height) in order to be readable. A minimum suggested text size would be around 3mm. Wherever possible, embossed or engraved text should ideally be facing away from the build plate, on the top layer of your component. Other post processing operations may be required to highlight and clarify small text.
It is possible for very short stretches of material, aligned horizontally to the build plate, to build without the need for support structures. In the world of 3D printing, this is called bridging. Lengths of up to 6mm can build without support, which is very useful when producing complex geometries.
Forgetting to give assemblies proper clearance is a common problem in design for additive manufacturing (DfAM). For mating assembly parts, we recommend a minimum clearance of 0.15mm is designed in. This will produce a interference fit. For a looser, sliding fit, use 0.2mm or 0.25mm. Parts designed to mate together with components fully assembled should print in a similar orientation, so that any warping affects both parts similarly. It is best practice to orient your designs so that the interfacing surfaces are vertical walls relative to the buildplate.
To avoid fragile features either not building, or immediately breaking, we recommend a general minimum feature size of around 1.5mm. In particular, check complex geometries carefully to ensure that no areas are thinner than this.