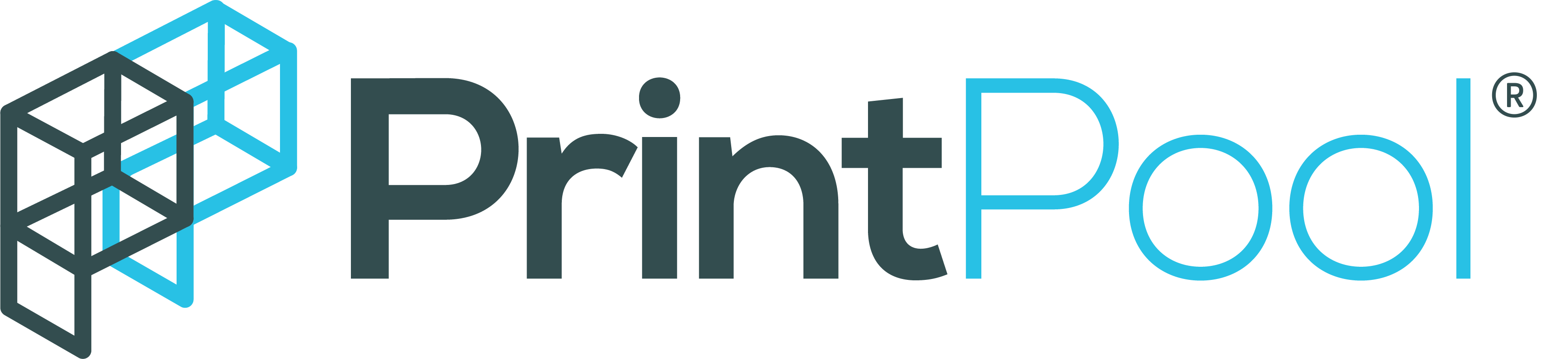
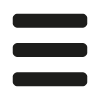
Fused deposition modelling (FDM) 3D printing, sometimes called Fused filament fabrication (FFF), or simply 'extrusion', is the most common type of additive manufacturing technology used globally. Nine times out of ten, if you speak to someone about 3D printing, FDM is the technology that they have in their head.
FDM 3D printing, as a manufacturing process, is very simple. A reel of filament (plastic wire) is fed into a hot nozzle (usually between 200-275°C) - which melts it. Molten material is then pushed through a precise nozzle, and deposited onto a flat surface, where it cools, forming a thin, solid pattern. The nozzle then moves up, relative to the surface, and the process repeats, so that another print layer of molten material is deposited on top of the previous one. As many thin layers build up on top of each other, your design is gradually produced.
A common analogy is that of a really expensive, complicated, and precise hot glue gun - and that is pretty much spot on. FDM printers extrude lines of material around 0.3-0.6mm wide, and 0.1-0.2mm thick.
We're not going to focus too much on the details of the technology however. Many, MANY articles have already been written on how to set up, troubleshoot, upgrade and otherwise tinker with FDM 3D printers. We're instead going to assume that you have access to a perfectly well-tuned, functional FDM 3D printer. This could be in-house, as part of a prototyping facility, or by using an outsourced manufacturing service.
However you go about using FDM 3D printers however, there are a few key FDM design considerations relating to of FDM 3D printing that you should be aware of in order to create great parts.
Components made using the FDM process are highly anisotropic. This means that the material properties in one direction are very different to those in another. In particular, the tensile strength of FDM materials is much less in the direction perpendicular to the layers. The bonds between layers are much weaker, because the previous layer was solid, and the current one, molten, when the bond was formed.
When these layers are put under stress, they have a tendency to rip apart, or delaminate, when subject to forces far lower than the tensile strength of the material itself. It is absolutely critical to bear this feature of the printing process in mind when designing FDM parts for functional use.
The best way to ensure that your parts are as strong as possible, and unlikely to break, is to ensure that any forces the part must resist, act only along the plane of each 'slice', and not through them. More advice on this is included in our 3D printing orientation article. If building parts that were designed generatively, make sure your study parameters take into account anisotropism, as the complex geometries that are produced using these techniques can otherwise be prone to failure.
Like many other forms of 3D printing, FDM components sometimes require the use of support material to help them build. Support material is use to create a support structure - a sacrificial platform upon which the component can be made. Generally speaking, any surface on your design that is at around 45° or steeper may need supports.
When support structures are removed from a component, they leave behind a scar on the surface they were in contact with. This is usually more pronounced the closer the surface was to the horizontal. Sometimes the scarring can be removed by post-machining operations or post manufacturing processes such as sanding the area manually, but this of course increases the cost.
Usually, when support structures are used they are made from the same material as the rest of the part. Dedicated support materials also exist however. Sometimes they are created so that they only bond weakly to the main build material, and so leave no obvious marks behind. Other types of support materials dissolve in water or other chemicals, making them easier to remove.
Great care should be taken when support materials are required around holes, delicate features, or internal channels, as it can be very difficult to remove them without damage to the component. Dissolvable support materials are often particularly useful in these cases.
Dissolvable support materials are also very useful when building complex geometries, such as those often produced as generative design outcomes.
Directly 3D printing is possible for sizes larger than M8, but they will not be as strong as machined threads, and would need a tap running through afterwards as a post processing operation. When designing built in threads, ensure that the 'modelled' option is activated in your CAD package.
We generally recommend the use of heat set inserts for smaller threads. The are small threaded brass inserts that can be heated up and pressed into the extruded plastic parts. Post processing operations like this can be expensive when there are multiple holes requiring threads on the same component, however.
It is also possible to directly tap some FDM materials. We recommend this for cosmetic parts that are not subject to significant stresses. Small threads produced in this way will fail quickly if subjected to heavy use.
Designers are sometimes taught to avoid adding unnecessary fillets to their designs, as they will increase the cost when machined or moulded. When designing parts for 3D printing however, this advice should normally be disregarded. Adding fillets and chamfers to sharp edges goes a long way towards making parts as strong as they can be.
Sharp edges, particularly when along layer lines, lead to large stress concentrations, and are almost always the focal point when 3D printed parts fail. Generally speaking, its good practice to add the largest possible fillet to all edges, where it won't interfere negatively with design features.
The only exception to this rule is on the first few layers touching the buildplate. Fillets on this surface can encourage air to circulate and therefore contribute to warping. They also require support structures.
We've discussed before how size is one of the most important factors that goes into pricing 3D printing work. Keeping your parts as small as possible has other benefits too.
Smaller parts have better tolerances generally, as any warping will have a smaller effect. Most 3D printing service providers express tolerances as a percentage of the dimension value, largely for this reason.
Keeping your part small will also mean that you have a larger choice of materials and machines available to you, as many 3D printers have a relatively small build volume.
The FDM printing process, when compared to other types of 3D printing, has the most visible layer lines. It also has the worst surface finish in most cases, particularly in areas where lots of support material is used to ensure that overhangs build correctly.
That being said, with proper design and a good understanding of the process, the surface finish of FDM printed parts can be made very good indeed. As with all DfAM (Design for Additive Manufacturing), the key is matching the process to the part, and vice versa.
Often, the best way to ensure good print quality is my minimising support material usage. We cover ways to do this in the next section. You will also get far better surface finish by avoiding shallow angles to the buildplate, and keeping as much of your design at 60° or more to the vertical.
The other factor affecting surface finish is layer height. All else being equal, a larger layer height will result in more visible 'stepping' - which is where the individual layers are very visible. Reducing the layer height will hide this effect, but also take longer to print, and so be more expensive.
The biggest cause of problems with the dimensional accuracy of parts is warping, but there is always a certain margin of error from other sources also. Most 3D printing providers guarantee ±0.2mm on most dimensions.
FDM 3D prints can sometimes warp during the printing process, or even sometimes after it has finished. This happens when some parts of the print cool faster than others. In general, areas of a design that are thinner, or located further away from the build plate will cool faster than thicker, denser areas located closer to the build plate.
Commonly this can be seen as the base layer curling away from the build plate, but other less obvious warping is also possible. Warping can affect the overall dimension tolerances of a component, as well as the flatness and straightness of surfaces and edges. High quality FDM parts can still be produced, and warping avoided, by using an industrial FDM machine, and following proper design practices.
When warping occurs during the printing process itself, it's usually caused by rapidly changing temperatures, such as when a breeze blows onto the part. This is one of the reasons that most good quality FDM 3D printers have a fully sealed enclosure, or doors added. High temperature gradients can also form between the first layer of a 3D printed part and the build plate. This is the main reason why good a FDM 3D printer has a heated bed - to reduce the temperature difference.
Warping that occurs after the print is finished usually occurs because the machine operator has tried to rush things. By removing FDM components from the machine too soon, the cooling process is accelerated, and they are far more likely to warp than if they were left to slowly return to room temperature. The slower the rate of cooling, the better.
Often materials that print at a higher temperature, and/or have a high thermal expansion coefficient are more prone to warping. This is the primary reason we don't print using ABS at Printpool, as ABS has both of these material properties. Tough PLA has similar strength, but is much more readily printable, which is why we prefer it.
Part design also has a role to play in warp prevention. Sharp edges, especially when located near the build plate, can encourage thermal stresses to concentrate, increasing the likelihood and severity of warping during the FDM process. This is because the part is being stretched in two different directions when cooling, exacerbating the stresses involved. We recommend generously filleting corners that are in contact with the buildplate, and aligned on the XY plane, to avoid this. Do not fillet edges that are aligned horizontally however. If there is no way to completely avoid sharp edges in your design, try and reorient the part so that they are not touching the buildplate.
Very dense and thick parts of your design will cool more slowly than thinner areas. For this reason, we recommend trying to have a consistent wall thickness throughout. A helpful rule when filleting edges, in order to create an approximately consistent thickness, is to make the fillet on the outer edge radius equal to the inner radius plus the intended wall thickness. Complex geometries produced using topology optimisation strategies often suffer less from warping issues, as the wall thickness is more constant.
FDM 3D printing has some unique features that make it different from other types of additive manufacturing technology. As such, the strategies and considerations in use when designing FDM parts are specific to the technology also.
We advise the following general order for designing parts to be made using FDM 3D printing. Feel free to share this with others, or to use it to explain design considerations to colleagues.
Note that when producing prototypes, that will eventually be made using other manufacturing processes, you can skip steps 3 to 6, as you should design your part for those processes, instead of 3D printing methods.
Without a good understanding of exactly what your part must do, it is impossible to design an effective component. Most times the clearer you are at this stage, and the better defined the use case is, the better the final part will be.
There are a wide variety of different FDM 3D printing materials available. Good 3D printing providers will work with you to identify the best materials for your application, and the very best (like us) may even buy in materials specially, when required, to meet your needs.
Sometimes it may turn out that the best material for you is actually an SLA 3D printing resin, or SLS powder. That's ok! It's better to know that at this stage than when you've already committed to designing for FDM 3D printing.
Traditional manufacturing has influences engineering designers a lot. You learn early on to produce cost effective components by making as few cuts into a solid billet of material as possible. This keeps manufacturing costs down, but only when using traditional manufacturing.
That is exactly what shouldn't be done here. The best way to design for an additive manufacturing process is to focus on designing in functionality first, and then add material slowly and reluctantly afterwards.
Using the example of a hole, using CAD model the correct size and depth. Only add the amount of material around the hole needed to make it practical and strong enough to work (maybe 5-15mm, depending on material). Leave this feature floating in free space as a separate body, and then move onto the next one - perhaps a complex surface that interfaces with the user's hand, or a battery housing. Again, use the minimum of material.
At this point you'll have a number of free floating bodies. The goal is now to connect them into a single component, using as little material as possible. For SLS 3D printing and SLA 3D printing, we often use generative design techniques at this point, but for FDM 3D printing its often best done manually. Although FDM printing can sometimes be used to manufacture complex geometries, SLS and SLA are often better suited to the task.
You'll probably have a blocky part now, that's just about in one piece. Further refine your design, by removing any material that doesn't fulfil a specific purpose or function.
By this point in the design process you should have a good idea of what orientation is best for your design. Look at the angles between surfaces and the location of key features. Think about what direction forces are likely to act, and how the part should be built with that in mind. Remember that hole orientation is particularly important.
Go back over your design with this orientation in mind. This can be an iterative process, and you may find that you change your mind about the print orientation as you go. Eventually however, you'll have a part that is optimised for a particular print direction, that prints with less support material, and is strong enough for use.
Some final design changes may be necessary to ensure that the specific printer you use, or your service provider uses, is happy with the size of all your features. Once this is complete you can export your design for manufacturing.
These guidelines are the ones we use to evaluate the feasibility of FDM 3D printing designs. Each service provider will have their own versions of these guidelines, but most are fairly similar.
The maximum part size we can print in one piece is 300mm x 200mm x 275mm. Other 3D printing providers, and machines, will vary. More expensive machines generally have a higher print speed which can make a big difference on large jobs.
We recommend a minimum hole diameter of 1.5mm if orientated vertically, and 2.5mm if orientated horizontally. When aligned along a horizontal axis, holes can be printed without supports when up to 6mm in diameter. It is more difficult to remove support material from blind holes, so bear this in mind when designing.
We recommend a maximum overhang angle of 45 degrees to print without supports. Overhangs of up to 90° will generally be printable, but will have a significantly poorer surface finish.
We have a suggested minimum wall thickness of 1.5mm for most FDM printing, on vertical walls. Horizontal wall thickness, where supports will be required, should be at least 2.0mm thick. Where a vertical wall connects to many other walls, you may be able to get away with slightly thinner designs, as each one is better supported.
Embossed writing or logos should be a minimum of 0.8mm thick, with at least 1.5mm of depth (or height) in order to be readable. A minimum suggested text size would be around 3mm. Wherever possible, embossed or engraved text should ideally be facing away from the build plate, on the top layer of your component. Other post processing operations may be required to highlight and clarify small text.
It is possible for very short stretches of material, aligned horizontally to the build plate, to build without the need for support structures. In the world of 3D printing, this is called bridging. Lengths of up to 10mm can build without support, which is very useful when producing complex geometries with FDM printers.
Forgetting to give assemblies proper clearance is a common problem in DfAM. For mating assembly parts, we recommend a minimum clearance of 0.15mm is designed in. This will produce a interference fit. For a looser, sliding fit, use 0.2mm or 0.25mm. Parts designed to mate together with components fully assembled should print in a similar orientation, so that any warping affects both parts similarly. It is best practice to orient your designs so that the interfacing surfaces are vertical walls relative to the buildplate.
To avoid fragile features either not building, or immediately breaking, we recommend a general minimum feature size of around 2.0mm. In particular, check complex geometries carefully to ensure that no areas are thinner than this.