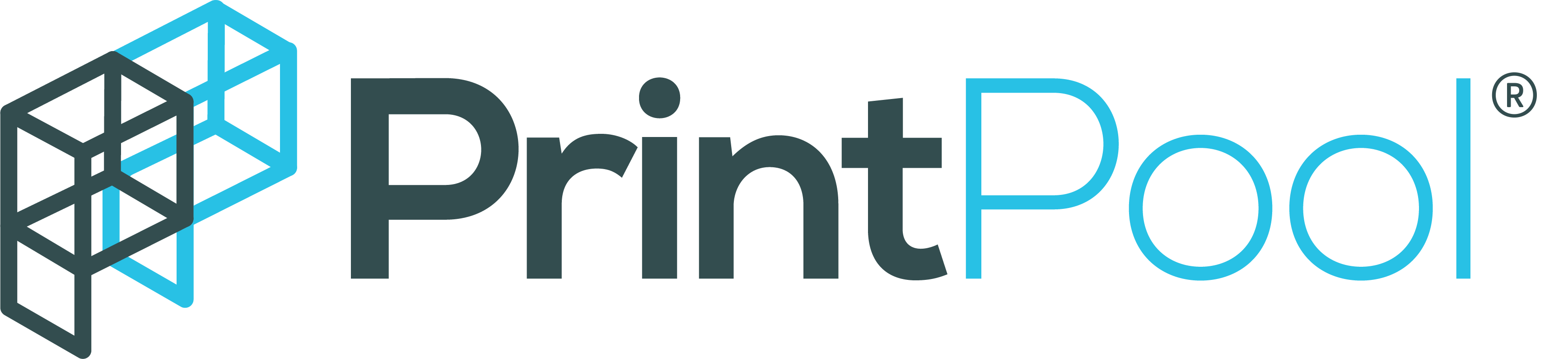
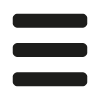
Choosing the right 3D printing material for your application is as important as choosing the right manufacturing process. Sometimes designers and engineers overlook this critical choice until too late in the process however.
A prototype made in the wrong material will be misleading. You may think that there is a problem with the function of your design, when in reality, the problem is with the function of the prototype itself. You may receive negative feedback from a client about the styling of your product, when actually, they just didn't like the finish or colour put in front of them.
End-use parts made in the wrong material are an even bigger problem. A part that breaks at the wrong moment can be dangerous, as well as frustrating. An rotating component that deflects an extra millimetre because its a hot day, could crash into other parts of a sensitive assembly.
Clear materials are very useful. Customers often find it helpful to see inside enclosures and casings, and useful demonstration models can be made using see-through 3D printing resins. Sometimes 3D printed parts can also be used for end-use applications. In particular, microfluidic models can be made very effectively using clear 3D printing materials, as it is useful to be able to see fluids move through the component. It is even possible to build complex parts for lenses and optics, but significant post-processing is usually required.
Although there are 'clear' FDM 3D printing materials available, they are firmly translucent, rather than transparent. This is mainly due to the FDM printing process, which produces tiny bubbles as the molten material is lain down. These bubbles stop light from travelling through the material.
The best option for clear materials is SLA 3D printing, or other resin based processes such as DLP. The smooth surface finishes associated with this technology cut down on post-processing, and the lack of bubbles or visible layers lines means light can pass through far more effectively.
Lengthy post-processing steps are required to create parts that are fully transparent. We do this by sanding parts using various grades of sandpaper, progressing from 400 grit to 5000 grit. The part is then polished and buffed to its final state. This is a labour intensive process, and only suitable for certain types of component, and very complex shapes may have surfaces that can't easily be reached.
Parts that will be mainly used outdoors must meet certain criteria. The exact requirements will of course vary depending on the exact application, but as a basic list, a material to be used outdoors, should:
Although not a particularly demanding set of requirements, a surprisingly large number of 3D printing materials do not meet this criteria. Many photopolymer resins, for example, are very susceptible to UV degradation, and often pose an environmental threat if not completely cured (and sometimes even then!). We never recommend SLA 3D printing materials for use outdoors, unless for very specific use cases.
Biopolymers such as PLA meet some, but not all of the criteria. Although fairly non-damaging from an environmental perspective, PLA performs poorly at high temperatures due to its low melting point. Ultraviolet light can also cause bleaching, and a decrease in mechanical properties over time.
The best materials for outdoor use are usually nylons. They are very stable across a wide-range of temperatures, and very UV resistant. We offer nylon materials as both SLS 3D printed parts, and CFR printed parts. PET-G is also a acceptable option, for when price is an important factor, as it can be made on an FDM 3D printer.
As 3D printing has become more widespread, the number of different industries that have begun to adopt the technology has grown. Printpool is a service provider, and we have also started to see an increase in the number of applications where chemical resistance is a critical factor when choosing the right 3D printing material.
The difficulty here, of course, is that chemicals are not all alike. Materials that are highly resistant to some types of chemical attack are often very susceptible to others. For example, although ABS (acrylonitrile butadiene styrene) shows excellent resistance to ethanol or hydrochloric acid, which would severely compromise other materials, it will completely dissolve in a matter of minutes if exposed to acetone (the main component in nail varnish remover).
This means that if you are planning a additive manufacturing application that involves chemical exposure, you should carefully check each chemical for compatibility with each material - very carefully. In broad terms though, it is still the case that some materials are more generally resistant than others. The best materials, generally, for chemical resistance tend to be nylons, such as Onyx, FBGR Onyx, or SLS Nylon.
SLA 3D printing resins are themselves made up of many different chemical components, to both enable the photopolymerisation reaction and give them their various mechanical properties. All these chemical constituents mean that the chance of one or more of them reacting with your substrate are higher than with other 3D printing materials, which are usually made up of just one or two chemical 'ingredients'.
High temperatures can be an important factor for 3D printed parts in automotive applications, but there are a range of other industries that need reliable parts for very hot environments. Unlike metal or ceramic parts, 3D printed polymers often have a melting point under 250°C, and can become softer and more flexible well below that.
Photopolymers used for SLA 3D printing often have particularly low temperature resistance, with a few exceptions. They are not thermoplastics, and so although they may soften as the environment gets warmer, they won't melt as such. Instead, resins generally begin to break down at high temperatures, and can even produce dangerous fumes. There are a few exceptions however. Formlabs produce a High Temperature resin, which can withstand a high temperature of around 200°C (we can order this material in on demand if required).
PLA has a low melting point. PET-G is somewhat better, but once again, the best options here are nylon based. Onyx, FBGR Onyx and SLS Nylon have excellent temperature resistance, and will remain functional right up to 120°C-140°C.
Before they are cured, when they are in their liquid state, SLA materials are not safe to handle at all. Once cured however, they are like FDM, SLS and CFR materials in that they are entirely safe to handle. Prolonged skin contact, over hours, days and weeks is another matter however.
Some materials, while safe to handle for short to moderate periods of time, may cause irritation, sensitising or even cytotoxicity when left in contact with the skin for long periods of time. This makes them unsuitable for use as medical devices, as well as other applications such as wearables.
All of our FDM 3D printing materials are skin-safe, as filaments. We still do not recommend FDM parts for long term skin contact however, as the layers, porosity and surface makes them prone to bacterial growth. This could cause harm for prolonged contact.
Similarly, our CFR materials, Onyx and FBGR Onyx, are unsuitable for prolonged skin contact, as Onyx can be a mild irritant if left in contact with the skin for long periods.
We have two materials that are suitable. The first, Tough 1500 Resin, is completely skin safe to ISO 10993 standards, once it has been completely cured (as it would be when parts using it are ordered from us). SLS Nylon is also skin safe, but we would only recommend it once it has smoothed - again to prevent bacterial build-up.
Shock absorption is an important attribute in additive manufacturing materials, and often overlooked. We have found that customers often request 'strong' parts, a trait which is associated with high tensile modulus. Materials such as glass however, that have high tensile strength, but low impact resistance can be less useful structurally.
Parts with good impact absorption, are usually referred to as durable, or tough, rather than strong. Materials such as FBGR Onyx can be both however. We recommend SLA materials such as Durable resin and Tough 1500 resin for applications that need high impact resistance and low stiffness/strength, SLS nylon and Tough PLA for applications that need high impact resistance and medium strength, and FBGR Onyx and Onyx for applications that need both high impact resistance and high strength.
It's worth bearing in mind that effective shock absorption is not defined by mechanical properties alone. 3D printers excel at producing complex topologies such as lattice structures - which can be tuned to absorb and dissipate impact forces far more effectively than convention materials. To print functional parts, that can withstand a high impact load, from 3D printed plastics is a challenge, but entirely possible.
3D printing is commonly used in architecture to produce models of buildings, neighbourhoods and even whole cities. This is very useful to help clients imagine what their building project will look like when complete, but also for light studies and to establish how a new building might affect the look and feel of an area.
The right material for the job depends on the type of model being created. When prototyping, or building quick mock-ups of large areas, FDM materials such as Recycled PLA would be perfect. Recycled PLA is very cost-effective for larger models, and comes in a range of colours to make different sections of the model stand out. Material properties and fine details aren't hugely important for this type of model.
For more detailed models of individual buildings however, we normally recommend Grey resin. This is a material that can capture fine details, and the smooth surface finish can produce stunning models. SLS materials can also be used to good effect more more complex structures that benefit from support-free printing.
There are a number of different reasons why 3D printing models of living things like animals, people, plants and even microorganisms can be useful. These types of models are commonly used in various hobbies, and also more serious applications in medicine and healthcare.
SLA resins are almost always the right 3D printing materials to choose in these cases, as organic shapes lend themselves very well to the SLA 3D printing process. Materials considerations like stress and heat resistance are unimportant here, so the smooth surface finish and unparalleled detail win out.
We don't recommend any 3D printing materials for food-safe applications. As mentioned earlier when describing skin-safe 3D printing materials, bacteria build-up in the pores and layer lines can pose a threat. In addition, SLA materials, which are less susceptible to this, are often chemically more dangerous to ingest.
There is a silver bullet here however. By using a hybrid process, we can get around the issue, and still benefit from the detailed manufacturing that additive methods provide. In the example shown here, we printed the design we wanted for what would become a custom chocolate bar. We then set a two-part, food-safe silicone around it. This mould is completely safe to use, as the silicone mould is washable, and can withstand high temperatures that will sterilise it. As we used an SLA master part, the effect of layer lines and porous areas was also much reduced. Tempered chocolate can now be poured into the mould, and when set, are perfectly safe for eating (and delicious).
Navigating the complexities of 3D printing materials can be difficult, even for very experienced engineers and designers who have a wealth of knowledge. As experts in the specific field of 3D printing and additive manufacturing, we can help you choose the right material for you, and your application. Get in touch today for a no obligation quote.