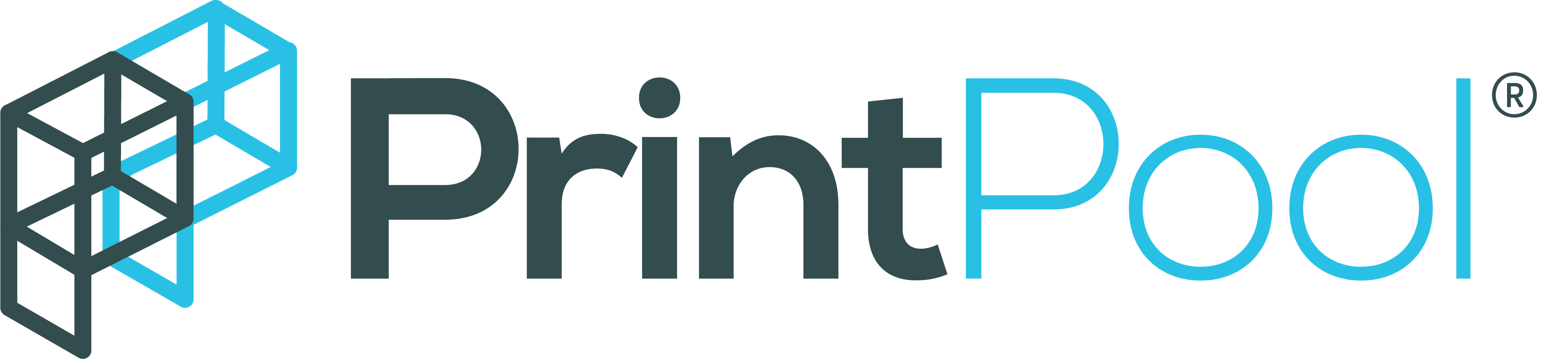
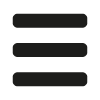
If we don't make big changes to the way that we live, quickly, then the world's climate will become increasingly less suitable for human life to flourish. Food scarcity, natural disasters, rising sea levels, and the catastrophic collapse of complex ecosystems will be an existential threat to billions of lives on this planet in the next 50-100 years, if nothing is done. A climate catastrophe such as this cannot be allowed to happen, and yet seems increasingly likely, due to the apathy of individuals, nations and corporations around the world. We all have a responsibly to play our part in preventing this terrible outcome.
The climate change crisis is caused by a runaway greenhouse effect. Energy from the sun travels through our atmosphere and hits the earth, and then is reemitted at a different wavelength by the earth's surface, before being reflected back at us by greenhouse gases in the atmosphere. This traps heat, and so the entire world gets a little bit hotter. To a point, this is a good thing. Without the greenhouse effect, our planet would be far too cold for us to survive. The problem is that since the industrial revolution this effect has been accelerated due too the production of huge quantities of carbon dioxide - which is a greenhouse gas.
The world is now getting hotter. We're rapidly approaching a point of no return, where These changes also interfere with complex weather systems and oceans currents - effects that climate scientists are only just beginning to understand - and lead to an ever-increasing threat from natural disasters such as hurricanes.
Preventing dangerous climate change, therefore, hinges on reducing the quantity of greenhouse gases like carbon dioxide in our atmosphere, and preventing more from being released. Right now, the global carbon footprint can be broken down into categories like this:
Another important issue is the problem of plastic pollution. Synthetic plastics are now found all over our world. They are in our oceans, forests, deserts, cities, and rainforests. Microplastics are now increasingly found in our rivers, food, and drinking water. Microplastics have even been found inside the womb, before a child is even born.
These plastics can be incredibly harmful to a wide variety of living things, including human health. Compounding the issue, many types of plastic don't easily break down, and so can remain whole for hundreds or thousands of years. As a species, we produce over 400 million tonnes of plastics every year. This is not sustainable.
Due to the nature of the additive manufacturing process, there are clear environmental advantages when compared to traditional manufacturing methods. Instead of starting with a solid billet (block) of material with subtractive manufacturing (milling, drilling, turning etc) and cutting away waste material - additive manufacturing starts with a blank slate, and builds up a component layer-by-layer, using only the material that is required to make the final part. This is far more efficient, as theoretically AM processes can be up to 100% efficient with material usage.
Sort of.
In reality, support materials are often required using some additive manufacturing processes, and even with the types of 3D printing that don't use supports, such as Selective Laser Sintering (SLS), there is still a percentage of material wasted. In a direct comparison however, traditional means of production are almost always less efficient than additive manufacturing in terms of raw material usage. Additive processes often have high energy consumption during the printing process, due to the high temperatures inside the machines.
While some polymer materials for FDM Printing can be made from recycled plastics, and can even be composted, it is far more difficult to create recyclable resins for SLA printing. UK company Photocentric has recently made some progress in this area however, which we are watching with interest. It is also important to note that many resins are considered toxic materials in their unprocessed state, particularly to aquatic life.
Our recycled PLA, supplied by Filamentive, is made from the factory waste streams. This recycled plastic material would otherwise go to landfill, but is instead diverted and used to print objects. This is possible with other materials also, but care must be taken to maintain the quality of the final product, as some the polymer-chains in some plastics can degrade with repeated processing.
It takes more energy to produce materials for 3D printing than it does to make metal billets for traditional manufacturing, as the raw metals must be atomised into fine, consistent metal powders prior to use.
Additive manufacturing (AM) excels at producing complex geometries. This means the benefits of techniques like generative design and topology optimisation, which tend to produce very complicated organic structures, can be realised. These methods make components and assemblies that are very light, and very light things require less energy to move. Less energy to move means less carbon emissions. Lattice structures, which can only be produced using AM methods, have a similar benefit.
It's important to carefully calculate these savings, taking into account the whole lifetime of the product. For example, if making a part via an additive process means that an extra 10kg of carbon dioxide is produced, but then over the lifetime of the component, 500kg of carbon dioxide are saved in comparison to a conventional component, then there is a clear benefit.
Some of the least environmentally friendly manufacturing processes are when products are made that are never used. Often, a high-fidelity prototype can help designers spot catastrophic errors that would result in a non-functional product, and therefore result in less material being used overall. Using a little extra material early on, to prototype a product effectively, can ultimately result in far less material being used overall.
Globally, manufacturing accounts for around 21% of greenhouse gas emissions. This is a huge percentage, and so optimising and improving the manufacturing sector's ability to make things efficiently will really help. Some of the carbon emissions are almost unavoidable with current technology, such as during steel making, because carbon is a critical 'ingredient' in the process. There are still ample opportunities for optimisation however.
Advantages in modern, digital manufacturing approaches can really have a big impact here.
14% of global carbon emissions are due to transport, and the majority of that is due to cargo ships, aeroplanes and HGVs. Moving goods from place to place is hugely wasteful, and can even seriously dent the environmental credentials of some otherwise 'green' products, like electric cars. If we can shorten the distance between where goods are manufactured and where they are sold/used, then a lot of this effect can be mitigated.
Digital manufacturing methods like 3D printing are well suited to distributed manufacturing approaches. This is where designs created anywhere in the world are sent to manufacturing hubs close to the point of use, and produced a short distance away from the end-user. This approach has huge benefits, and as the machine 'instructions' for 3D printing are can be created remotely, is perfectly plausible. A shorter supply chain is a happy side-effect.
Some people take this idea a step further, and imagine that in the future, households may each run a 3D printer and produce the goods they need under their own roof (at Printpool, we reckon this is pretty farfetched, though).
As many 3D printing processes can take place without direct human supervision, lights-out manufacturing is entirely possible in additive facilities. In fact, Printpool runs 24/7 manufacturing operations, despite only being staffed for around 6-8 hours per day.
With no people present, manufacturing facilities don't need to use power for heating, lights or other utilities that human beings require in order to be comfortable. Operating with a small in-person workforce also saves on the need for commuting. This has a clear benefit of reduced carbon emissions.
At Printpool, we think the climate crisis is the single biggest issue facing the world today. Things need to change, and although personal carbon footprints are important, we think that governments and companies have the biggest responsibility, and the potential for the biggest impact. Every business has a responsibility to reduce their energy consumption / total carbon footprint, and in doing so, target a more sustainable future.
At Printpool, we have a number of environmentally conscious practices that reduce energy usage and raw materials use, and so lower our carbon footprint, while maintaining a high quality production process that makes great parts.
We will continue to improve our environmental practices as time goes on, and we learn more about the best ways forward.
Our most eco-friendly material is Recycled PLA, which is also compostable using industrial facilities. Bear in mind that additive manufacturing technologies have many other environmental benefits however.
For every 3D printed part that you order with us, we will plant an real tree, typically in mangrove forests in Madagascar. We also offset all of our staffs' carbon footprint using Gold Standard certified carbon offsets, and use recyclable and recycled materials where possible.